1. HET ONTSTAAN VAN DE KATOENINDUSTRIE
Katoen was zonder enige twijfel een onmisbare grondstof geworden. Het kon voor verscheidene doeleinden gebruikt worden en was geliefd omdat het zacht aanvoelde en goed absorbeerde. Toch werd katoen tot twee eeuwen geleden niet veel gebruikt in onze streken. We gaan even terug in de tijd.
In Egypte werden op mummies stoffen terug-gevonden, die waren vervaardigd uit bijzonder fijn linnen dat meesterlijk was geweven. Naar alle waarschijnlijkheid waren de Egyptenaren ook bekwame textielververs, aangezien een aantal van deze stoffen met tekeningen was bedrukt.
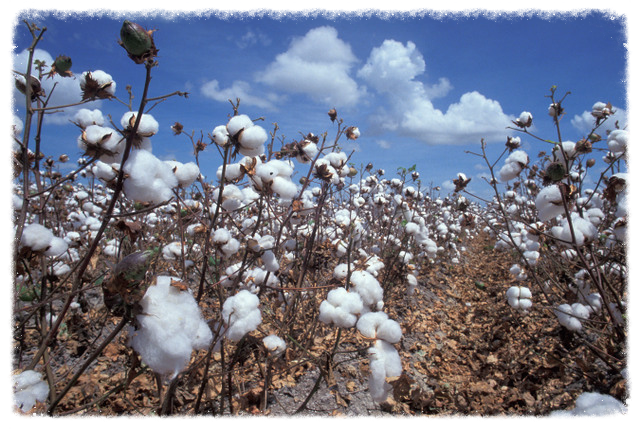
De Grieken en de Romeinen hielden dan weer voornamelijk van wollen stoffen, die ze rechtstreeks op de huid droegen. Dit zorgde geregeld voor huidirritaties, die de Romeinen verzachtten door vaak te baden.
Pas vanaf de eerste helft van de Middeleeuwen begonnen de mensen linnen ondergoed te dragen, zodat de wollen stof de huid niet meer prikkelde.
Blijkbaar was het gebruik van katoen helemaal niet bekend bij de beschavingen rond de Middellandse Zee, Egypte, Fenicië, Griekenland en Rome. Dit is verbazingwekkend, temeer omdat zij in de vroege Oudheid al geregeld contact hadden met India, waar sinds mensenheugenis katoen wordt geteeld, gesponnen en geweven. Ook op mummies van de Inca’s in Peru werden katoenstoffen teruggevonden.
Katoen dook voor het eerst op in Vlaanderen in de 14de eeuw.
Het kwam uit het Oosten. In de kerk werden bijzonder fijne katoenen stoffen gebruikt tijdens de erediensten, en werden waardevolle religieuze voorwerpen in katoenen watten gewikkeld.
Toch waren het voornamelijk de eerste Europese ontdekkingsreizigers, die katoen bij ons introduceerden. Bedrukte katoenstoffen, die werden verkocht als “indiennes”, waren elegant en stevig, maar ook goedkoop. De “indiennes” werden snel populair en men begon ze in grote hoeveelheden in te voeren vanaf het midden van de 17de eeuw.
2. DE INVOERING VAN DE KATOENINDUSTRIE IN GENT
Op het einde van de 13de eeuw was Gent de belangrijkste lakenstad van Europa. De stad telde zo’n 60.000 inwoners, waarvan bijna de helft in de lakenindustrie werkte.
In het midden van de 14de eeuw kende de lakenverkoop een terugval door de forse concurrentie uit Italië en Frankrijk. De linnenindustrie nam op dat moment een hoge vlucht, vooral dankzij de aanwezigheid van de Leie, die uitermate geschikt bleek voor het roten. In Gent waren het de vrouwelijke kloosterlingen, en dan met name de Kapucijnernonnen, die zich toelegden op de vlasspinnerij.
Op het einde van de 17de eeuw voerden Frankrijk en Engeland massaal katoenstoffen in uit India,
en daarna nam Engeland de controle over de grondstoffen van Indigo in Indië om ze te laten spinnen en weven in Manchester. De Oostenrijkse regering probeerde ondertussen op alle mogelijke manieren de handel en industrie in ons land nieuw leven in te blazen.
Het bedrukken van katoenstoffen was een bloeiende industrie bij onze noorder- en zuiderburen, en de Oostenrijkse regering trachtte die ook bij ons te introduceren. België kreeg de wind in de zeilen toen het Engelse parlement een reeks wetten uitvaardigde (1701, 1720 en 1736) om de invoer van katoenstoffen terug te dringen en zo de eigen linnen- en wolindustrie te beschermen.
De Oost-Indische Compagnie kon maar moeilijk Indische stoffen verkocht krijgen in eigen land en ging deze daarom vrij verkopen in de meeste havens op het Europese vasteland. Via Amsterdam kwamen de stoffen en gesponnen draden in België terecht.
Pas rond het midden van de 18de eeuw vestigde zich in Gent een tak van de katoenindustrie, die wel degelijk succesvol bleek te zijn : men ging katoen bedrukken om de “indiennes” na te maken, die zo in de mode waren.
In 1760 vestigde Quirin Vleminckx uit Antwerpen zich in Gent om er de “kunst van het verven en glanzen van katoen” te beoefenen, “iets wat niemand hem ooit had voorgedaan in Gent”.
Vleminckx stelde meer dan 60 arbeiders tewerk. Op zijn verzoek stelden de schepenen hem in 1763 vrij van een aantal heffingen die door de stad werden geïnd.
Ook andere handelaars startten katoendrukkerijen op. De belangrijkste waren de vennoten François Lousbergs en C.F. Villot (1785) en Frans De Vos en Abraham Voortman (1791).
Zowel François Lousbergs als Abraham Voortman waren Nederlandse textielverkopers, die zich in Gent hadden gevestigd.
François Lousbergs huwde op 24 juli 1717 met Marie Catharina. Haar vader François Villot was de eerste Gentenaar die in 1767 “indiennes” bedrukte.
Abraham Voortman werd vennoot van Frans De Vos, de schoonbroer van Lieven Bauwens.
3. DE AUTOMATISERING VAN DE GENTSE KATOENINDUSTRIE
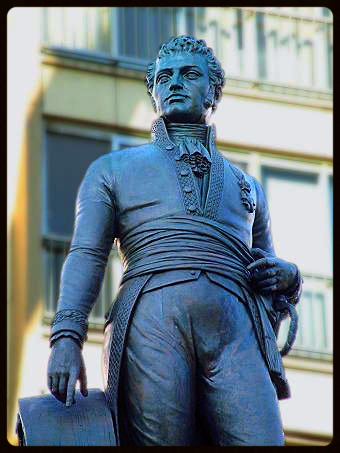
De automatisering van de Gentse katoenindustrie is verbonden met de persoon van Lieven Bauwens, die werd geboren in een familie van leerlooiers.
Lieven maakte in Engeland kennis met textiel-fabrikanten en katoendrukkers. Hij was zo onder de indruk van de nieuwe automatische spinmachine “Mule Jenny”, dat hij ze wilde invoeren. De “Mule Jenny” kon 1300 maal meer draden produceren dan een machine die met de hand werd bediend. Voortaan zouden geen draden en stoffen uit India meer ingevoerd moeten worden maar wel enorme hoeveelheden katoenbollen.
De invoerhandel van Lieven Bauwens diende als dekmantel om gedemonteerde machines uit Groot-Brittannië binnen te smokkelen op het vasteland (1798). Lieven werd echter betrapt door de Britse politie en verloor het grootste deel van zijn materieel. Toch slaagde hij erin een fabriek in Passy op te starten (1798) met de hulp van Engelse arbeiders die hij had omgekocht.
LIEVEN BAUWENS
Omdat hij een fervente aanhanger van Napoleon was, kreeg Lieven de steun van de Eerste Consul, en werd hij verkozen als eerste burgemeester van Gent. Hij richtte verschillende fabrieken op in Gent (1801) en in Drongen (1799). De bedoeling was zijn fabricagemethodes wijd te verspreiden (C.F. Villot, De Vos en Bauwens).Tussen 1800 en 1809 ging het de Gentse spinnerijen voor de wind.
Daar kwam in 1810 verandering in, toen de Gentse katoenfabrieken zich omwille van de Engelse blokkade maar moeilijk konden bevoorraden.
Lieven Bauwens werd zwaar getroffen door de diepe economische crisissen. Hij was geruïneerd door het einde van het Franse keizerrijk en stierf in 1822 in Parijs als een arme man.
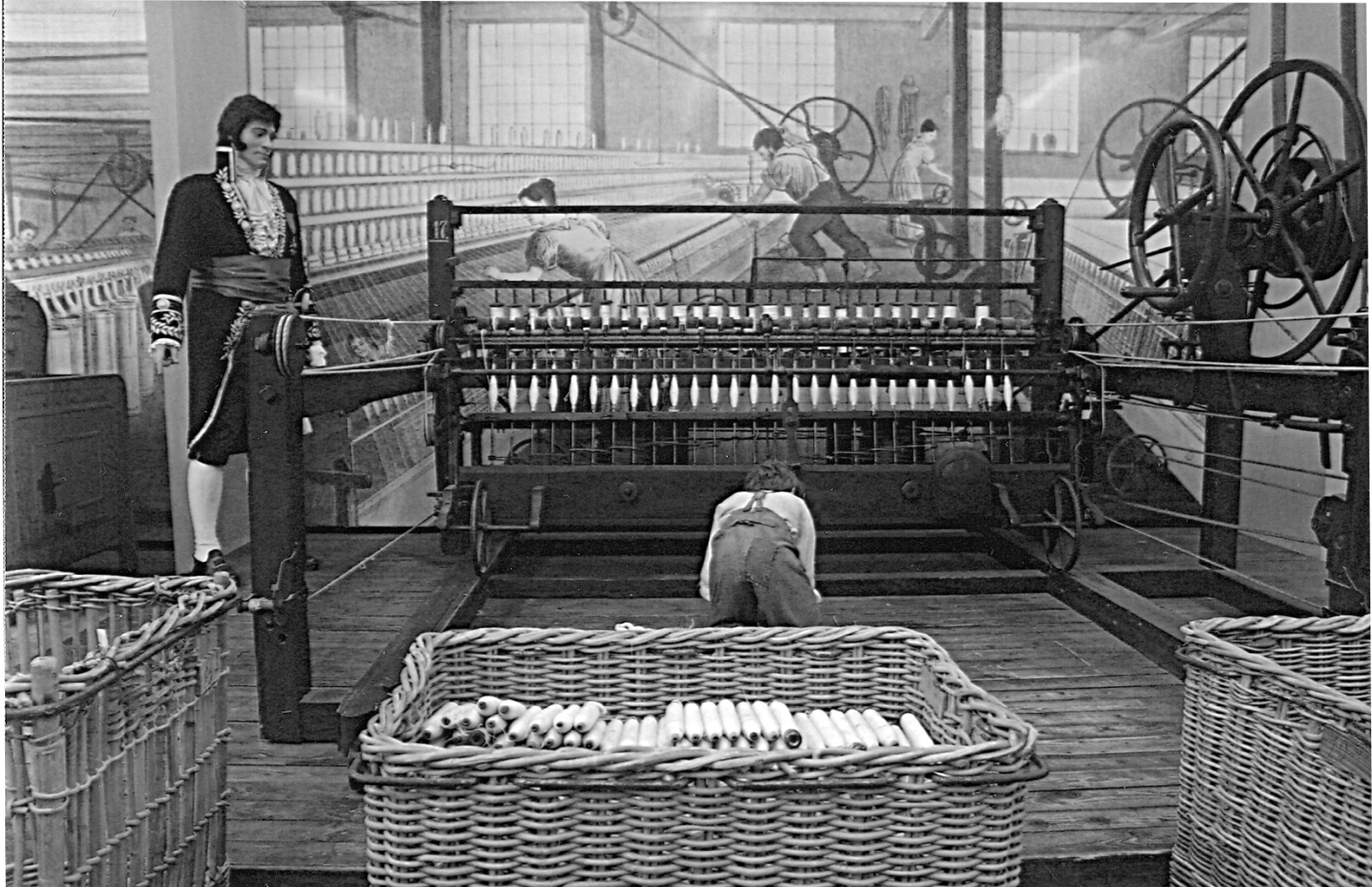
SPINMACHINE "MULE JENNY" in het MIAT-museum te GENT
4. DE GROTE BLOEI VAN DE GENTSE KATOENINDUSTRIE ONDER NEDERLANDSE VOOGDIJ
Op 28 juni 1814 bepaalde het protocol van Londen dat België en Nederland zouden worden verenigd. Deze beslissing werd in 1815 bekrachtigd door het Verdrag van Wenen.
De eenwording kondigde een nieuwe periode aan in de economische geschiedenis van ons land.
Met de ineenstorting van het Franse keizerrijk verloor België een afzetgebied van 40 miljoen gebruikers.
Tot dan toe ging onze industrie nog nooit gebukt onder protectionistische maatregelen. De Belgische industrie had uitsluitend handelsbetrekkingen met Frankrijk en was speciaal toegerust om deze markt te bevoorraden.
Na de eenmaking van België en Nederland sloot de Franse markt zich volledig af voor deze twee landen. Frankrijk hield onder de republikeinse regeringen en tijdens de Restauratie vast aan het colbertisme. Er werd een tolmuur opgericht en angstvallig werden alle buitenlandse producten geweerd. De verschillende industrietakken in ons land leden onder deze politiek.
Waar Vlaanderen tot dan 90% van het linnen had geleverd voor Frankrijk, kwam er nu niet één stuk stof de grens meer over.
België hoorde nu bij Nederland, een land waarmee we voordien maar weinig handelscontacten onderhielden.
Onze katoenindustrie was aan haar lot overgeleverd en zat diep in de problemen. Door de buitenlandse concurrentie kon ze amper het hoofd boven water houden.
Onze nieuwe bestuurders zagen aanvankelijk niet in dat zij maatregelen moesten nemen om onze katoenindustrie te beschermen en het voortbestaan ervan te garanderen.
In Gent was de situatie schrijnend. De meeste fabrieken lagen stil, de rest draaide niet op volle kracht. Er werd minder loon uitbetaald en de arbeiders konden nauwelijks de eindjes aan elkaar knopen. Vele arbeiders waren verhuisd naar het noorden van Frankrijk, waar zich een nieuwe textielindustrie begon te ontplooien.
Koning Willem I van Nederland was er zich van bewust dat het erg gesteld was in onze streken en vaardigde in 1822 een reeks wetten uit om de industrie te beschermen.
Zo kwam hij op het voortreffelijke idee om twee instanties op te richten die van groot belang zijn geweest voor de ontwikkeling van onze industrieën.
Allereerst stichtte hij in 1822 de “Generale Bankmaatschappij ter Begunstiging van de Handel en de Industrie”, die een opmerkelijke invloed had op onze industrie. De bedoeling was dat deze maatschappij zou fungeren als discontobank, spaarbank en commanditaire bank.
De maatschappij was vooral actief in de metaal- en steenkoolindustrie. Dankzij haar steun en haar fondsen namen deze een hoge vlucht en kon Wallonië zich industrialiseren. De textielindustrie kon echter op weinig aandacht rekenen.
De koning van Nederland richtte nog een tweede instelling op : de “Nederlandsche Handelsmaatschappij”. Deze bestaat nog steeds bij onze noorderburen en heeft er dezelfde functie als de Generale Maatschappij in België.
Officieel moest de Nederlandsche Handelsmaatschappij de handel tussen moederland en kolonies stimuleren. Met de regering werd echter een geheim contract gesloten om een deel van het budget (11 miljoen gulden) in de textielindustrie te investeren.
Zo konden dankzij de Nederlandsche Handelsmaatschappij, katoenstoffen uitgevoerd worden naar Nederlands-Indië, waar de vele inwoners al geruime tijd katoenen kleding droegen.
Vóór 1815 kwam 1/8 van de stoffen uit Nederland en 7/8 uit Engeland, ondanks protectionistische maatregelen (25% van de invoer) voor de Nederlandse producenten.
In 1829 keerden de kansen en was bijna 90% van de stoffen afkomstig uit het Gentse.
De koning van Nederland liet gereedschapsmachines uit Engeland komen om de vervaardiging van textielmachines te verbeteren bij Phoenix in Gent (katoen) en de in 1817 opgerichte “Établissements Cockerill” (wol).
Hij gebood eveneens over te gaan tot de aanleg van het kanaal Gent-Terneuzen om de haven van Gent verder te laten ontwikkelen.
Al deze koninklijke initiatieven zorgden ervoor dat de Belgische industrie één van de welvarendste was op de vooravond van de revolutie van 1830.
De Gentse katoenindustrie was uitgegroeid tot de belangrijkste van het Europese continent.
Het België van 1829 was niet meer te vergelijken met het België van 1814 : er heerste een opvallende bedrijvigheid. De bekkens van Bergen, Charleroi en Luik waren bezaaid met steenkoolmijnen en geavanceerde hoogovens. De lakenindustrie had van de koning een monopolie gekregen voor de uitrusting van het leger en het burgerlijk bestuur, waarop nieuwe fabrieken verrezen langs de oevers van de Maas en de Vesder. Doornik zag zijn oude tapijt- en porseleinproductie herleven. De schatkist raakte flink gevuld dankzij nieuwe fabrieken, die werden opgericht en oude die herop leefden.
De bevolkings aangroei van een stad is een teken van de vitaliteit van haar industrie. In 1815 telde Gent 62.220 inwoners, in 1830 waren dat er al 79.800.
Toen Willem I in 1829 de belangrijkste steden van het land bezocht, werd hij overal enthousiast ontvangen. Vooral in Gent werden kosten nog moeite gespaard toen handelaars en fabrikanten, het stadsbestuur en ook de universiteit de koning verwelkomden op 29 mei.
Verschillende verenigingen lieten zich van hun meest patriottische kant zien: de industriële verenigingen, de Concorde, de gildevoorzitters en vooral de Schutterij. Deze laatste was recent heringericht en werd bestuurd door de elite van de Gentse adel en de bourgeoisie (1500 man).
De verjaardag van de koning op 14 augustus 1829 werd met veel luister gevierd.
5. DE ONTWIKKELING VAN DE KATOENINDUSTRIE VAN 1830 TOT 1914
Het onafhankelijk België werd een land met twee gezichten.
Het zuiden ontwikkelde zich tot de meest geïndustrialiseerde regio in de wereld na Groot-Brittannië. De groeipolen situeerden zich rond de steenkoolmijnen en de metaalindustrie van Luik en Henegouwen.
Brussel werd de financiële hoofdplaats van het land. Daar waren de Generale Maatschappij en de Bank van België gevestigd, twee instellingen die controle uitoefenden op de industrie en kapitaal injecteerden door naamloze vennootschappen op te richten.
Het noorden van het land richtte zich op de landbouw, met uitzondering van de Gentse textielindustrie.
De breuk met Nederland betekende voor de katoenindustrie een ware ramp.
Na de onafhankelijkheid verloor die immers haar belangrijkste klant, Nederlands-Indië. De zoektocht naar nieuwe markten werd belemmerd door de protectionistische maatregelen en tolkosten, die de buurlanden oplegden.
De Vlaamse katoenindustrie verloor niet enkel haar Nederlandse klanten, maar zag zich ook gedwongen op een beperkte markt te concurreren met de sterke Engelse industrie. Onze katoenindustrie bleek onvoldoende geautomatiseerd en was gedoemd om te verdwijnen.
Gent was de enige stad, die de concurrentie met het buitenland aanging. Ze investeerde in nieuwe weefgetouwen en in 1840 ook in spinmachines op spincontinu, die de oude Mule Jennymachines van Lieven Bauwens moesten vervangen. De nieuwe machines draaiden sneller en produceerden fijnere en sterkere draden.
Het weef- en spingereedschap werd steeds vaker aangedreven door stoommachines.
Alle inspanningen ten spijt was men toch genoodzaakt de lonen te verlagen en de mannelijke arbeiders te vervangen door vrouwen en kinderen.
Fernand Lousbergs (1799-1859) had erg snel begrepen dat hij moest innoveren om zijn zaak draaiende te houden.
In Lyon maakte hij kennis met Jacquard (1752-1834), een uitvinder van weefgetouwen. Jacquard had een automatisch weefgetouw uitgevonden, waarbij elke kettingdraad apart werd aangestuurd door een ponskaart. Dankzij deze nieuwe techniek konden stoffen vervaardigd worden met uiterst ingewikkelde patronen.
Het weefgetouw werd op punt gesteld rond 1831. Vanaf dat moment kocht Fernand Lousbergs regelmatig een hoeveelheid machines aan tot hij er in 1842 in totaal 350 bezat.
De meeste van zijn machines bevonden zich aan de Reep. Daar kocht hij in 1823 het oude klooster van de Kapucijnernonnen, die bekend stonden als vlasspinsters. De draden voor het weefgetouw waren afkomstig van de nieuwe spinnerij, die hij in 1830 optrok aan de Reep. De oude fabriek van de familie aan de Molenaarstraat had hij afgestaan aan zijn schoonbroer Felix de Hemptinne.
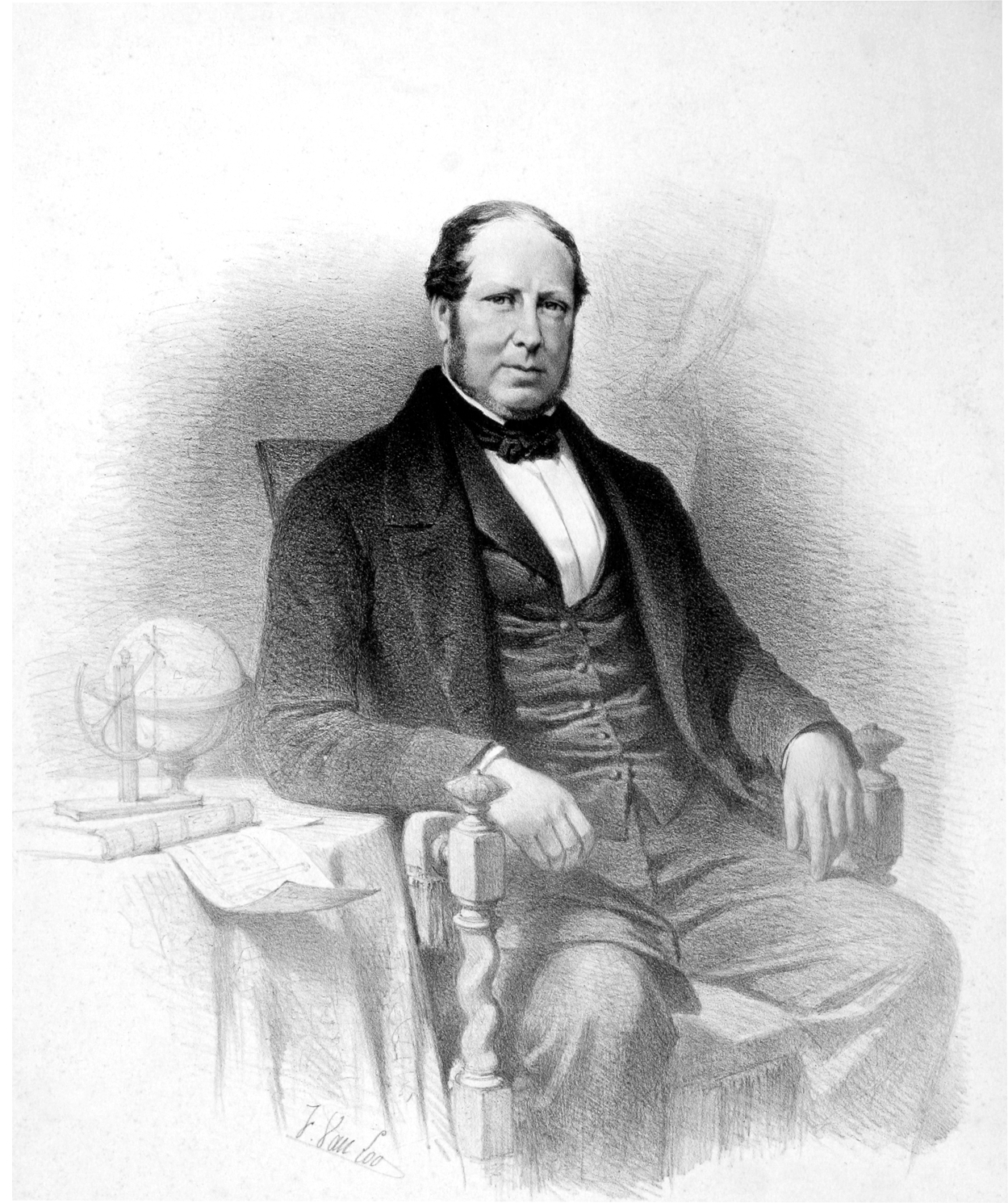
Fernand Lousbergs (1799 - 1859)
Foto: De Zwarte Doos
Fernand Lousbergs was één van de eerste Gentenaren die beschikte over weefgetouwen met stoomaandrijving.
In 1852 bezat hij niet enkel de grootste textielfabriek van België maar ook de modernste.
In 1856 startte hij een gigantische spinnerij op met 40.000 spillen om 400 Jacquardweefgetouwen van draad te voorzien. Toen hij in 1859 stierf, was Fernand Lousbergs de grootste textielfabrikant van het Europese vasteland.
Hij liet aan de stad Gent een bedrag na van 400.000 BEF samen met enkele gronden aan de Visserij, om een tehuis te bouwen voor ouderen en gehandicapte arbeiders. De familie de Hemptinne (Charles en Jules) erfde zijn fabriek aan de Reep.
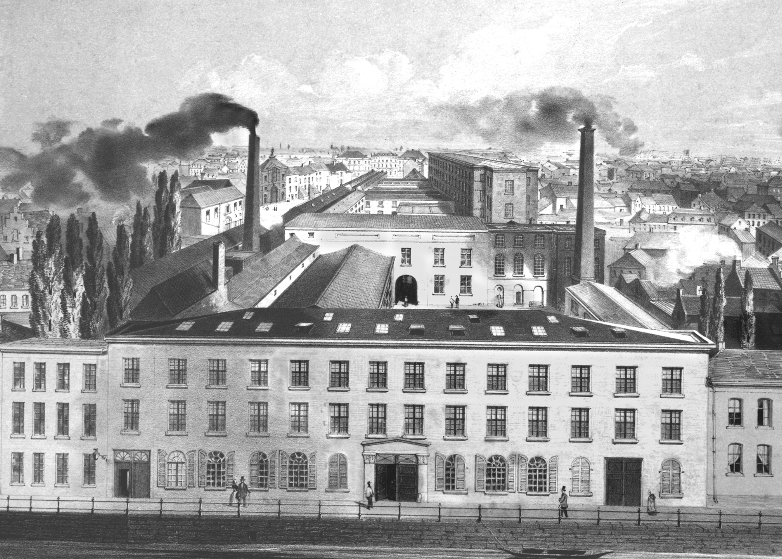
FABRIEK en HUIS aan de REEP van FERDINAND LOUSBERGS
Foto: stadsarchief GENT, De Zwarte Doos, Foto Storm Calle
De andere belangrijke industriëlen hadden gekozen om te investeren in de mechanische vlasspinnerij, die in Engeland was ontstaan.
Rond 1829 liet John Cockerill in Luik een zeer grote fabriek bouwen, van 7 verdiepingen, op de gronden van een voormalig convent van de recolletten. Hij installeerde er een mechanische vlasspinnerij en noemde de fabriek "La Liniére Cocquerill". De directeurs van de fabriek waren respectievelijk vader Edmond Benoit Lardinoit en zoon Edmond Louis Lardinoit.
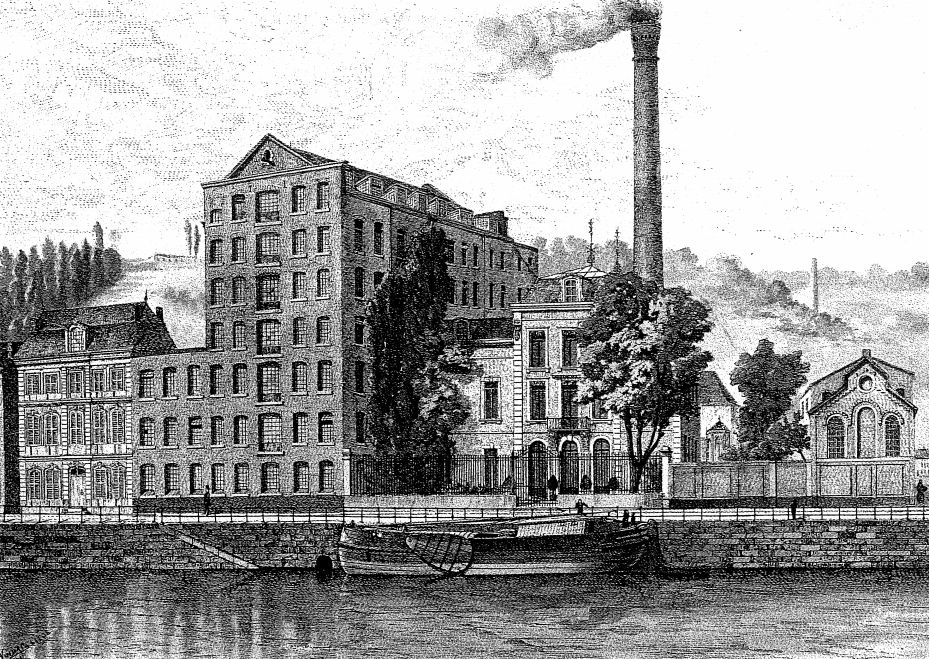
Société linière de Saint-Leonard
Een zakenman en bankier, afkomstig uit Wetteren en wonende te Gent, François-Louis LEIRENS (*), kocht in 1839 La Linière Cockerill van John Cockerill, en veranderde de naam in "Société linière de Saint-Leonard". Eén jaar daarvoor, in 1838, financierde Leirens, samen met de Generale Maatschappij, de eerste Gentse mechanische vlasspinnerij "La Lys".
* François Louis Leirens was de zoon van Englebert Ignace Leirens, de notaris te Wetteren, die de akte verleed, waarbij in 1805 burggraaf Vilain XIIII het klooster aan de groene Briel te Gent, aan de Vogelenzang, met blekerij en gebouwen verkocht aan Abraham Voortman voor zijn drukkerij, voor de som van 6000 frank in goud.
Société Linière La Lys
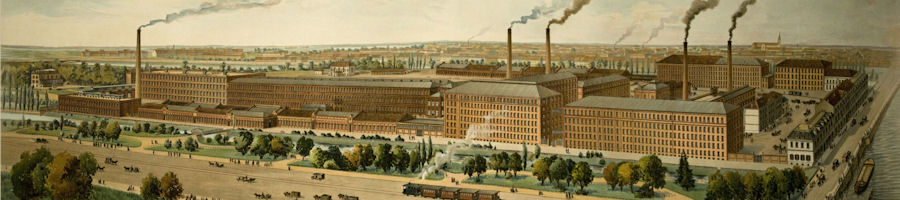
Het bedrijf, waar mechanisch gesponnen vlas- en hennepdraden vervaardigd werden, werd opgericht op 6 juni 1938 door Felix-Joseph de Hemptinne. Het werd grotendeels gefinancierd door reeds genoemde François-Louis Leirens en de Generale Bankmaatschappij.
Zo was François-Louis Leirens een van de voornaamste aandeelhouders .
In 1840 trouwde zijn dochter Eugénie Leirens met Eugène de Smet (later de Smet de Naeyer)
Zo werd Eugène de Smet bestuurder van
Société Linière
La Lys en La Linière de Saint-Leonard.
Veel later werd Fernand de Smet de Nayer, de zoon van Eugénie Leirens, voorzitter van de raad van bestuur van Société Linière
La Lys.
Nochtans blijft het bedrijf
Société Linière
La Lys bestuurd door de familie de Hemptinne.
Na "
Société Linière
La Lys" kwamen in Gent een groot aantal vlasbedrijven bij.
De voornaamste waren:
- Linière Gantoise
- Linière Saint-Sauveur
- La Liève, opgericht in 1866 en beheerd door de familie Voortman.
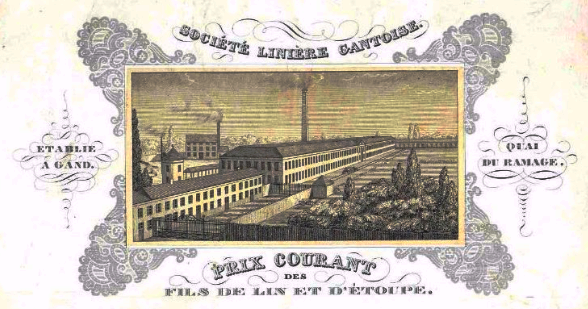
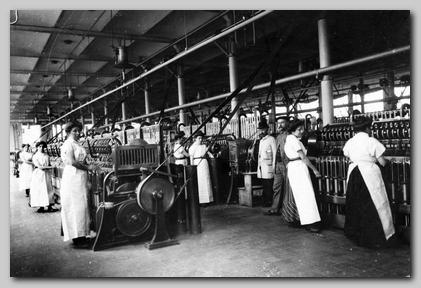
Société Linière GANTOISE Société Linière La Lys
De mechanisering van de vlasindustrie vernietigde het thuiswerk. Talrijke vlasspinsters in de boerderijen (± 10 000) verloren zo een onmisbaar inkomen.
De slechte oogsten van de jaren 1844-1846 maakten de ellende ondraaglijk. Vlaanderen werd “Arm Vlaanderen”. De migraties namen toe, met name naar de industriebekkens van Wallonië en naar de Gentse industriewijk. Ondanks de harde levensomstandigheden, konden de fabrieksarbeiders beter overleven dan de boeren of de dagloners op het platteland.
De grote massa werkzoekenden liet de Gentse industriëlen toe hun arbeiders een hongerloon te betalen.
Huisvestingsmaatschappijen maakten eveneens van de situatie gebruik door in de onmiddellijke omgeving van de fabriek arbeiderswoningen te bouwen van 5m. bij 5, zonder sanitair, stromend water of elektriciteit.
De arbeiders hadden de mogelijkheid niet om te staken, omdat de wet Le Chapelier, van kracht sinds 1830, hen verbood zich te verenigen. Iedere inbreuk werd bestraft met een boete of een gevangenisstraf.
De arbeiders konden niet rekenen op de regering, want die werd geleid door een elite, verkozen door 2% van de bevolking via het cijnsplichtig stemrecht.
Door de Secessieoorlog in de Verenigde Staten (1861-1865) ondervond de Gentse katoenindustrie grote bevoorradingsproblemen.
De stopzetting van de katoenleveringen leidde tot talrijke faillissementen. 2000 arbeiders emigreerden naar Noord-Frankrijk als gevolg van de werkloosheid in onze streken.
Op het einde van de 19de eeuw kon de katoenindustrie zich enigszins hernemen. De katoenfabrieken werden gedecentraliseerd. Sommige fabrieken verlieten de stad Gent en vestigden zich op het platteland of in kleinere steden waar de arbeiderslonen lager waren en de macht van de vakbonden minder groot.
De snelle toename van het aantal spinnerijen op het einde van de 19de eeuw had een bittere en uitputtende concurrentie tot gevolg, die het bestaan zelf van de Belgische katoenspinnerij bedreigde. Die crisis mondde op 4 oktober 1894 uit in de oprichting van de “Association cotonnière de Belgique”. Zij had als belangrijkste taak de prijzen vast te leggen, de verkoopsvoorwaarden gelijk te schakelen en de productie te beperken.
Op initiatief van haar voorzitter, graaf Jean de Hemptinne, ontstond in 1904 de “Fédération Internationale cotonnière”.
Om zich op een moeilijke toekomst voor te bereiden, reorganiseerde de vereniging van de spinners zich in mei 1917 in een coöperatieve maatschappij die ze sindsdien behouden heeft.
Diverse organisaties - De “sociale werken” van de Association Cotonnière de Belgique.
De Association Cotonnière de Belgique creëerde nog andere organismen of speelde een vooraanstaande rol in de oprichting van andere belangenverenigingen. Die organisaties (zie hieronder voor meer details) droegen bij tot de oprichting van Febeltex (de Belgische Textielfederatie) en Securex.
- De Lonencommissie bestond uit industriëlen en legde de arbeidsvoorwaarden vast in samenspraak met de arbeiderssyndicaten.
- De Fédération Patronale des Industries Textiles des Flandres zorgde voor een band tussen de textielgroepen in de streek. De werking van de federatie lag aan de basis van de “Caisse Centrale d’Assurance Mutuelle des Textiles des Flandres contre le Chômage involontaire“. Deze kas werd in 1924 opgericht (door Charles Christophe, de stichter van Securex) en werd ook de “Caisse de Grèves Christophe” genoemd, die de bazen moest beschermen tegen verplichte werkloosheid. Ze werd overgenomen door Febeltex in 1982. Jacques De Porre was de laatste voorzitter.
- De Caisse commune d’Assurance mutuelle contre les Accidents de Travail (“Les Industries textiles réunies”) werd gesticht op 11 januari 1905 door Charles Christophe en ligt aan de oorsprong van Securex.In 1928 verzekerde dit organisme 76.000 textielarbeiders en ongeveer alle katoenondernemingen van het land maakten er deel van uit.
- De Association Textile, Caisse d’Allocations familiales (ATCAF) werd opgericht in 1926 en was een vereniging zonder winstoogmerk. Deze zeer actieve vereniging fuseerde in 1970 met de “Algemene Compensatiekas voor Gezinstoelage van Oost-Vlaanderen” en in hetzelfde jaar met Securex. De laatste voorzitter van de ATCAF was Jacques De Porre.
-
7.DE AUTOMATISERING VAN DE GENTSE KATOENINDUSTRIE VAN 1914 TOT
1940 EN FERNAND HANUS
Tijdens de oorlog van 1914-1918 hadden de Duitsers de goederen en de machines van de Gentse katoenfabrieken geplunderd. De fabrieken op het platteland waren gespaard gebleven. Die situatie bracht de Gentse katoenfabrieken ertoe te fuseren en/of een beroep te doen op de banken.
In 1919 fusioneerden de fabrieken Galveston (van de familie Braun), Desmet-Guéquier (van de familie Hebbelynck) en Jules de Hemptinne. Ze werden in hoofdzaak gefinancierd door de Generale Maatschappij en hadden als belangrijke schuldeisers de “arbeiders-curatoren”. De nieuwe onderneming heette N.V. Union Cotonnière en had als voorzitter Gérard Cooreman (voormalig Eerste minister en gouverneur van de Generale Maatschappij). De onderneming werd geleid door baron Emile Jean Braun (voormalig Galveston) en door Adolphe Hebbelynck (voormalig Desmet-Guéquier).
Fernand Hanus werd zes maanden later aandeelhouder door de inbreng van een nieuwe spinnerij, wat van hem de grootste aandeelhouder maakte samen met de Generale Maatschappij.
Vanaf 1920 kende de Gentse katoenindustrie een grote bloei.
De Union Cotonnière kocht twee spinnerijen (de Spinnerij van Rooigem en de Cotonnière de Gand) en vier nieuwe weverijen (Cruypelandts, Ter Platen, …)
1923 : Aline Hanus-De Landtsheer (de zus van Fernand Hanus) kocht 1/3 van de aandelen van de N.V. Texas.
1933-1934 :Wereldwijde economische crisis.
Door de beurscrash van Wallstreet in New York in 1929 geraakten verschillende katoenondernemingen in moeilijkheden. De grote onderneming van Fernand Lousbergs werd opgedoekt. De gebouwen werden verkocht aan de Zusters van Liefde en omgedoopt tot de Sint-Bavohumaniora.
1937-1938 : Nieuwe economische crisis. De export werd afgeremd om de volgende redenen :
1° De landen die aankochten voor de oorlog van 1914-1918 (India, Japan, Zuid-Amerika, …) waren van hun leveranciers afgesneden door Duitsland en waren verplicht zelf hun textiel te produceren.
2° Sterk geïndustrialiseerde landen die niet door Duitsland bezet waren, beschikten over moderner materiaal en waren concurrentiëler (Engeland, Italië, Frankrijk).
A) Fernand Hanus, pionier van de nieuwe Vlaamse textielindustrie (1880 - 1924)
Vanaf het begin van de 20e
eeuw was
het
ontegensprekelijk Fernand Hanus, die de grootste invloed had op de katoenindustrie, dit zowel op sociaal vlak als op de industriële vooruitgang.
Samen met zijn zus Aline lag hij aan de basis van de latere fusie van de 3 grote Gentse textielbedrijven.
Ten gevolge van de samenwerking tussen de research afdeling in UCO Hanus Laarne en de hogeschool en universiteit kwam UCO van 1968 tot 1989 aan de top van de Europese textielindustrie.
De talrijke uitvindingen en realisaties van UCO hebben nog altijd een invloed op de textielindustrie.
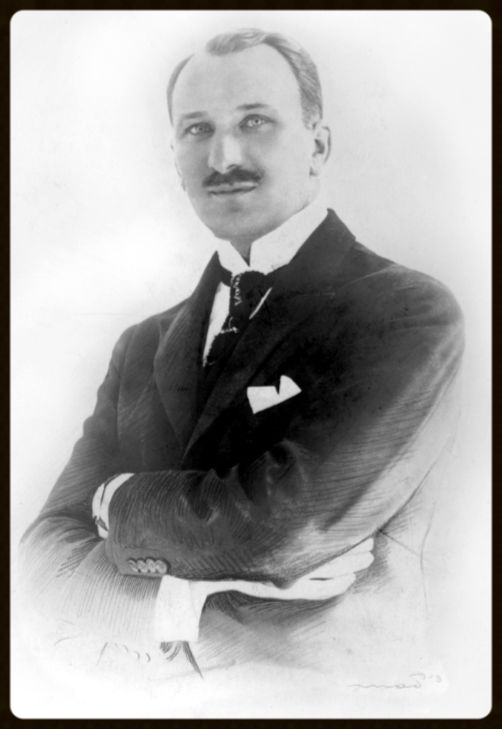
Fernand Hanus werd geboren in Gent op 16 november 1880. Zijn vader, Ernest Hanus, was een textielhandelaar die zijn grondstoffen kocht in Engeland en liet loonweven in de omstreken van Gent. De afgewerkte producten werden verkocht in de gehele wereld via zijn winkel in de Drabstraat.
Zijn zoon Fernand (1880-1924) besliste om zelf over te gaan tot de productie van stoffen en koos resoluut voor de industrie. Hij studeerde bijgevolg textiel en scheikunde.
In 1900 bouwde hij de eerste weverij op de site van de voormalige abdij van Oudenbos, die zijn vader in 1883 had gekocht (Zeveneken-Lokeren). In de nabijheid van zijn weverij bouwde hij een ververij. Dankzij de spoorlijn tussen Gent en Antwerpen was het gemakkelijk de waren in de streek te vervoeren.
In tegenstelling tot de Gentse textielbazen die voornamelijk over spinnerijen beschikten, concentreerde Fernand Hanus zijn activiteiten op de weverijen en de afgewerkte producten (verven en finishing) en dat was trouwens zijn sterkte.
Fernand Hanus wou met katoen de warmte-eigschappen van wol nabootsen. Hij heeft een Duitse constructeur gevonden die met naalden de katoenstoffen wolachtig kon maken.
Hij wou zelf de controle hebben over de kwaliteit van de katoendraden en kocht in 1905 een grote fabriek in Laarne, die spinnerij, weverij en veredeling (verven en finishing) integreerde. Hij voegde er een grote lainageafdeling aan toe. Deze “lainage” was wereldwijd bekend en het Franse leger was zeer geïnteresseerd in de kwaliteit van die stoffen.
Om officiële leverancier te worden moest Fernand Hanus echter in Frankrijk produceren. Daarom kocht hij twee fabrieken in Frankrijk, in Sotteville-les-Rouen (de vroegere vestiging Bertel) en in La Lande Clecy. (confectie)
In 1914 verklaart Frankrijk de oorlog aan Duitsland. Fernand Hanus voorzag dat Duitsland zeer waarschijnlijk België zou binnentrekken en de fabrieken zou plunderen. Daarom bracht hij al de grondstoffen en weefsels van de fabrieken van Oudenbos en Laarne onder in een depot van zijn vader in Londen.
Hij stelde zijn zuster Aline Hanus, die
de aankoop deed van grondstoffen voor haar vader, aan als verantwoordelijke voor zijn grondstoffen en afgewerkte producten in Engeland.
Vervolgens nam hij Edmond Lardinoit aan, de gewezen directeur van de Linière St Leonard, als verantwoordelijke voor zijn fabriek in Frankrijk, die spoedig de uniformen aan het Franse leger zou leveren.
Gedurende de oorlog 1914-1918 maakte Fernand Hanus geweldig veel winst door zijn verkoop van uniformen aan het Franse leger en door de verkoop van zijn voorraden in Engeland
Fernand Hanus was sociaal vooruit op zijn tijd.
Fernand Hanus was een vader voor zijn arbeiders en hij waardeerde ze in dezelfde mate als zijn directe medewerkers. Hij nam niet enkel hun materiële maar eveneens hun intellectuele noden ter harte. Zonder enige politieke motieven liet hij in de onmiddellijke omgeving van zijn industriële vestigingen talrijke, elegante arbeiderswoningen bouwen, die voorzien waren van tuintjes en het nodige comfort, zoals stromend water en elektriciteit.
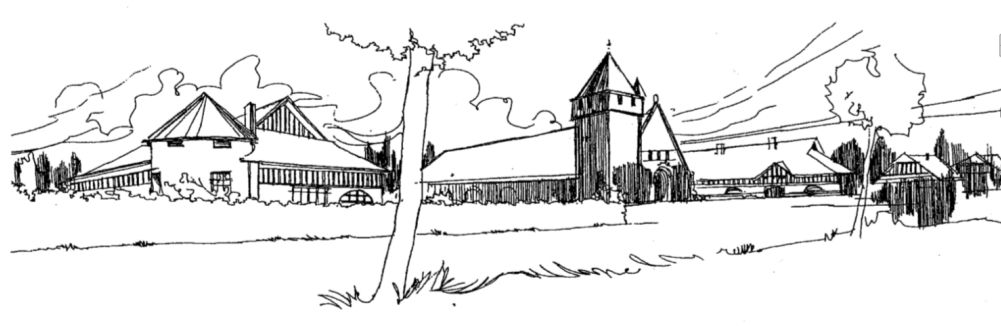
Dorp Fernand Hanus naast de fabriek
In de buurt van de fabriek van Oudenbos (Lokeren) stichtte hij een bekoorlijke wijk in Normandische stijl, met een basisschool voor jongens en voor meisjes, een klooster, een kerk, een pastorie, een verblijf voor de onderwijzers, enzovoort. Iedere fabriek werd voorzien van een dispensarium, dat geleid werd door een gediplomeerd verpleegster.
Fernand Hanus was de eerste in de textielsector, die zijn eigen elektriciteit fabriceerde voor de verlichting van de fabriek. Daardoor kon er ook ’s nachts geproduceerd worden.
Door de invoering van een ploegensysteem hoefden de arbeiders niet langer te werken dan 10 uur per dag. Fernand Hanus was er namelijk van overtuigd dat een tevreden arbeider ook beter werk leverde. In 1920 richtte hij een coöperatieve op, die door het fabriekspersoneel beheerd werd en die voorzag in hun basisbehoeften. De coöperatieve bevatte tevens een ziekteverzekering, “De Goede Overeenkomst”, die in geval van werkongeschiktheid een vervangingsinkomen uitkeerde.
Dit paternalisme is verder doorgevoerd door zijn zoon en kleinzoon, tot COBEPA in 1985 bij UCO gekomen is. “De Goede Overeenkomst” is in 1997 gefuseerd met de ziekteverzekering PARTENA.
De onderneming Fernand Hanus financierde dit goede doel met aanzienlijke bedragen. Bovendien schonk zij aan alle leden gratis een lijfrente vanaf 65 jaar, een uitkering bij overlijden en een uitkering vanaf 60 jaar voor arbeiders, die voor hun dertigste in dienst waren getreden.
Fernand Hanus was vooruitstrevend op industrieel vlak.
Fernand Hanus was de eerste in de textielwereld in België die over een eigen elektrische centrale beschikte. Dat was nodig opdat de arbeiders ook ’s nachts zouden kunnen werken. Het is zo dat hij de eerste was in de Belgische textielsector die het ploegensysteem invoerde.
Zijn grootste realisatie was het maken van katoenweefsels met de warmte eigenschappen van wol. Hij heeft een Duitse machineconstructeur gevonden, die met naalden de katoen wolachtig kon maken (laineermachine). Dit gelaineerd weefsel dat gefabriceerd werd in een groot geïntegreerd bedrijf, werd wereldwijd verkocht. Ook het Franse leger was sterk geïnteresseerd zodat Fernand Hanus een fabriek voor dit soort weefsel liet bouwen in Rouen en een confectie in La Lande Clecy. Dat was nodig om de uniformen te leveren aan het Franse leger voor de oorlog 1914-1918. Deze kleren in geruwd katoen waren even warmer als wol en hadden het voordeel in natte toestand te verhogen in sterkte, in tegenstelling tot wol dat zijn sterkte verliest als het nat wordt.
Het gelaineerde katoenweefsel werd ook gebruikt voor het polijsten van glas op een continu glasinstallatie, een nieuw revolutionair procedé van GLAVERBEL. Dankzij dat weefsel werd hij een belangrijke leverancier aan de glasindustrie.
Fernand Hanus was een man met geniale visies; bij het uitbreken van de eerste wereldoorlog dachten de meeste textielindustriëlen dat het conflict van korte duur zou zijn; Fernand Hanus dacht echter het tegendeel. Daarom liet hij al zijn grondstoffen en afgewerkte producten verschepen naar Engeland. Gezien de Engelse vloot na troepen te hebben afgezet op het continent, leeg terugkeerde naar Engeland kostte dit vervoer weinig of niets aan Fernand Hanus; en voor het geval het conflict toch van korte duur zou zijn kon hij zijn grondstoffen en afgewerkte producten, die ondertussen schaars geworden waren, even goedkoop terug naar het vasteland laten brengen aangezien de schepen anders leeg naar het vasteland moesten komen om de troepen terug op te halen. Fernand Hanus won dus in beide hypotheses
In 1920 bracht hij zijn machinepark in bij de Union Cotonnière, die in grote moeilijkheden verkeerde en gefinancierd werd door de Generale Maatschappij. Zo werd Fernand Hanus, na de Generale Maatschappij, de grootste aandeelhouder van de Union Cotonnière.
In 1923 kocht hij het Flandria Palace Hotel, dat gebouwd was in het teken van de Wereldtentoonstelling van Gent. Bedoeling was het kantoor en de winkel van de Drabstraat daar onder te brengen.
B) De automatisering van de Gentse katoenindustrie van 1914 tot 1940 en Fernand Hanus
Tijdens de oorlog van 1914-1918 hadden de Duitsers de goederen en de machines van de Gentse katoenfabrieken geplunderd. De fabrieken op het platteland waren gespaard gebleven. Die situatie bracht de Gentse katoenfabrieken ertoe te fusioneren en/of een beroep te doen op de banken.
In 1919 fusioneerden de fabrieken Galveston (van de familie Braun), Desmet-Guéquier (van de familie Hebbelynck) en Jules de Hemptinne. Ze werden in hoofdzaak gefinancierd door de Generale Maatschappij en hadden als belangrijke schuldeisers de “arbeiders-curatoren”. De nieuwe onderneming heette N.V. Union Cotonnière en had als voorzitter Gérard Cooreman (voormalig Eerste minister en gouverneur van de Generale Maatschappij). De onderneming werd geleid door baron Emile Jean Braun (voormalig Galveston) en door Adolphe Hebbelynck (voormalig Desmet-Guéquier).
Op het einde van oorlog dacht hij dat zijn fabriek in Laarne geplunderd zou zijn en kocht hij in Engeland materiaal voor een nieuwe spinnerij. Bij zijn terugkeer in België stelde hij vast dat de fabriek in Laarne in goede staat was gebleven. Daarom bracht hij het spinnerijmateriaal in 1920 over naar de Union Cotonnière, die in grote moeilijkheden verkeerde en gefinancierd werd door de Generale Maatschappij.
Zo werd Fernand Hanus, na de Generale Maatschappij, de grootste aandeelhouder van de Union Cotonnière.
Hij ontwikkelde in belangrijke mate de fabrieken van Laarne en Oudenbos, omdat hij wou dat zijn eigen fabrieken de eerste textielonderneming van België werden.
Vanaf 1920 kende de Gentse katoenindustrie een grote bloei.
De Union Cotonnière kocht twee spinnerijen (de spinnerij van Rooigem en de Cotonnière de Gand) en vier nieuwe weverijen (Cruypelandts, Ter Platen, …)
In 1923 kocht hij het Flandria Palace Hotel, dat gebouwd was in het teken van de Wereldtentoonstelling van Gent. Bedoeling was het kantoor en de winkel van de Drabstraat daar onder te brengen.
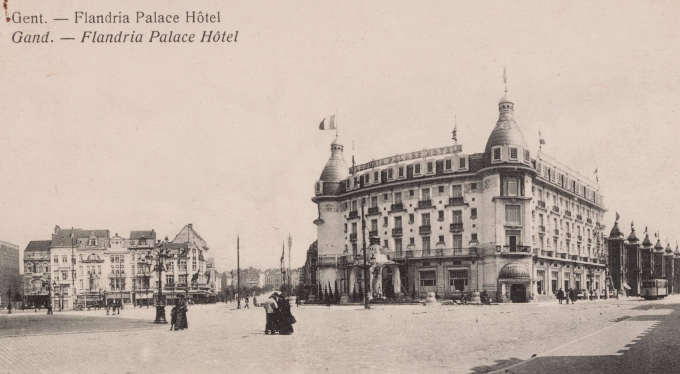
1923 : Aline Hanus-De Landtsheer (de zus van Fernand Hanus) kocht 1/3 van de aandelen van de N.V. Texas.
Aline Hanus had, samen met haar broer Fernand Hanus, veel geld gewonnen met het beheren van het depot in Londen. Daarmee richt zij een grootwarenhuis op aan de Korenlei in Gent.
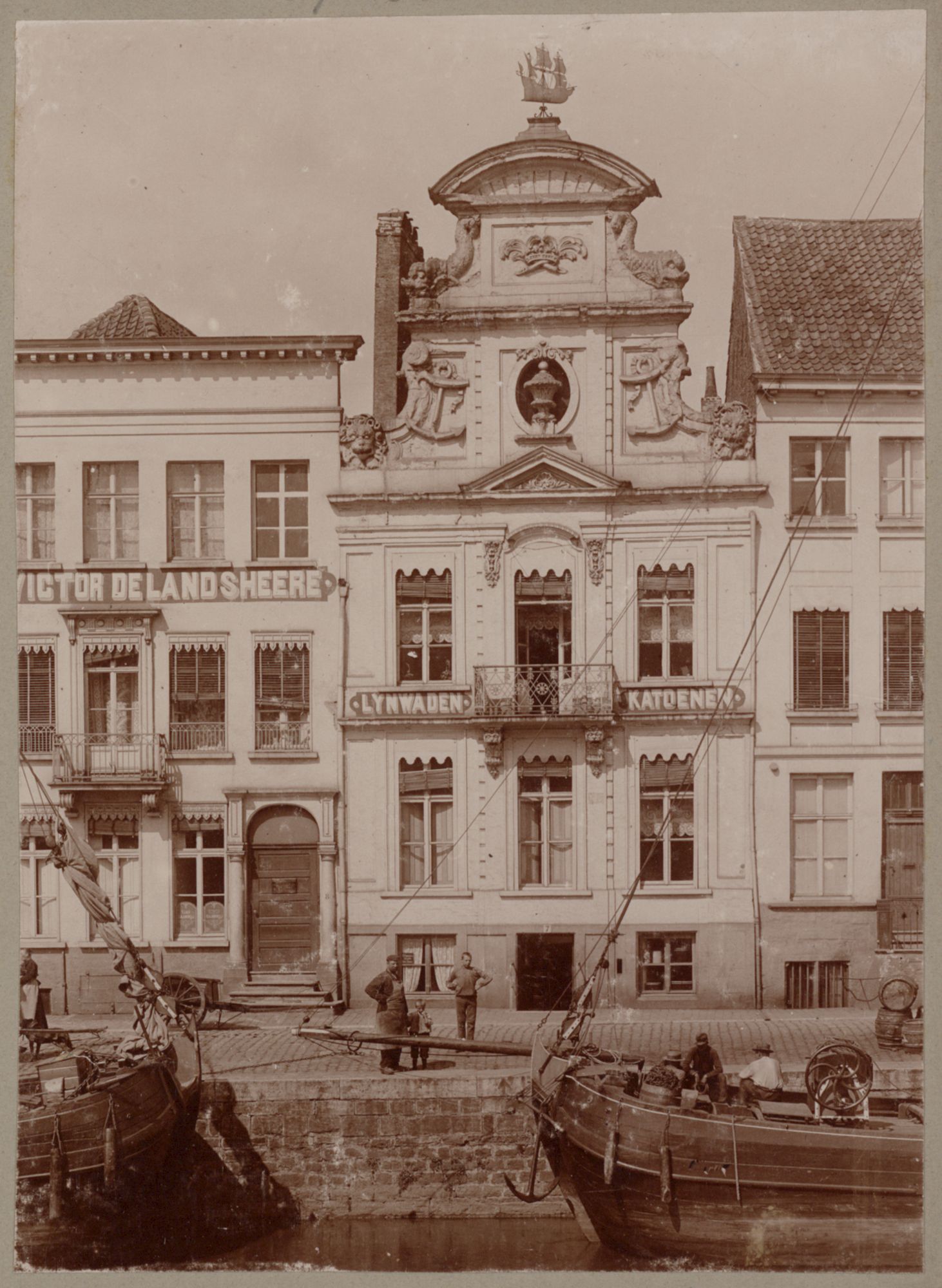
In 1923 wou ze industrieel worden zoals haar broer Fernand Hanus. Daarvoor kocht zij van Jules Voortman 1/3 van de aandelen van de nv. TEXAS.
De directeur generaal van TEXAS was
Edmond Lardinois, gewezen directeur van de Etablissements BERTEL s.a. Hij werd vervangen in Bertel door de heer en mevrouw Julien. (Mevrouw Julien was de secretaresse van Fernand Hanus).
In 1926 nam Jacques Voortman, kleinzoon van Jules Voortman, de leiding over in de nv. TEXAS.
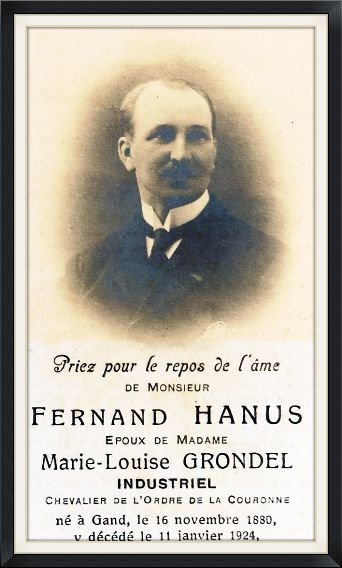
Op 11 januari 1924 bezweek Fernand Hanus op 43-jarig
e leeftijd aan de gevolgen van een bloedvergiftiging. Hij liet een vrouw en drie zonen na : Albert (20 jaar), Georges (19 jaar) en René (18 jaar). Zodra het bericht van zijn overlijden bekend was, eisten de banken de terugbetaling van de hoge investeringskredieten. Zijn erfgenamen zagen zich gedwongen het Flandria Palace en de landgoederen in Frankrijk te verkopen om de torenhoge erfeniskosten en de terugbetaling van de kredieten te bekostigen.
De oudste zoon Albert zette zijn studies burgerlijk ingenieur stop en nam de leiding van het bedrijf op zich. Zijn broer Georges werd verantwoordelijk voor de verkoop van de stoffen.
In 1925 werd de onderneming Fernand Hanus een naamloze vennootschap, waarvan het voorzitterschap werd waargenomen door de weduwe van wijlen Fernand Hanus, Marie-Louise Grondel.
Gedurende de crisisjaren werd de Franse vestiging Bertel verkocht. In 1931 nam de jongste zoon René (Hanus) Hanet de bedrijfsleiding over. Dankzij zijn spinnersopleiding in het Franse Roubaix en verschillende stages in de VS had hij een gedegen kennis verworven inzake katoennijverheid.
1933-1934 :Wereldwijde economische crisis.
Door de beurscrash van Wallstreet in New York in 1929 geraakten verschillende katoenondernemingen in moeilijkheden. De grote onderneming van Fernand Lousbergs werd opgedoekt. De gebouwen werden verkocht aan de Zusters van Liefde en omgedoopt tot de Sint-Bavohumaniora.
De Nouveaux Etablissements Bertel worde verkocht maar de heer en mevrouw Julien blijven de onderneming beheren.
1937-1938 : Nieuwe economische crisis. De export werd afgeremd om de volgende redenen :
1° De landen die aankochten voor de oorlog van 1914-1918 (India, Japan, Zuid-Amerika, …) waren van hun leveranciers afgesneden door Duitsland en waren verplicht zelf hun textiel te produceren.
2° Sterk geïndustrialiseerde landen die niet door Duitsland bezet waren, beschikten over moderner materiaal en waren concurrentiëler (Engeland, Italië, Frankrijk).
DE KATOENINDUSTRIE VAN 1945 TOT DE FUSIE VAN DE DRIE GROOTSTE GENTSE TEXTIELBEDRIJVEN (NV UCO) en de nakomelingen van FERNAND HANUS.
In tegenstelling tot wat er gebeurde in WO I, bleven de Gentse textielbedrijven gespaard van plunderingen door de Duitsers tijdens de Tweede Wereldoorlog. Vlaanderen werd slechts weinig het slachtoffer van bombardementen, in vergelijking met de rest van Europa. Van 1945 tot 1950 kende de Gentse katoenindustrie dus een grote bloei.
Na de oorlog werd de katoenindustrie beïnvloed door verscheidene gebeurtenissen.
1) De opkomst van synthetische vezels maakte het mogelijk kreukvrije, meer scheurbestendige en rotvrije stoffen te vervaardigen.
2. Na de onafhankelijkheid van de Aziatische landen (India, Pakistan) werd Europa overspoeld door katoenen stoffen. Landen met plantages, zoals Turkije, raakten geïndustrialiseerd dankzij het Marshallplan. Zij leverden kwaliteitsvolle draden en stoffen. Tussen 1960 en 1970 kreeg de Gentse katoenindustrie het hierdoor zwaar te verduren.
3) De communistische landen van Oost-Europa verkochten hun katoenproducten aan dumpingprijzen teneinde vreemde deviezen te verwerven.
Om de belangen van de textielindustrie beter te verdedigen werd in 1948 Febeltex (de Belgische Textielfederatie) opgericht. Zij werd voorgezeten door Robert Brasseur en vertegenwoordigde de 29 verschillende economische textieltakken van het land (katoen, vlas, veredeling, …) en de 7 sociale werkgeversorganisaties (Gent, Verviers, …).
Na de oprichting van de EEG (1957) werd in 1962, op initiatief van de katoenwever Charles Uyttenhove, de vereniging van Europese textielindustrieën Comitextil uit de grond gestampt. Comitextil verdedigde de belangen van de textielsector (de Multivezelovereenkomst, …) en werd vertegenwoordigd door de Europese voorzitters van de diverse textieltakken (Eurocoton, CRIET, …) en door de voorzitters van de textielfederaties van elk land (Febeltex, Fenitextil, …).
Hoe de drie grootste katoenfabrieken op de nieuwe uitdagingen hebben gereageerd
Union Cotonnière
De Union Cotonnière werd beheerd door:
- Als voorzitter de heer Lambert van de Société Generale
- Als ondervoorzitter de heer René Hanet die ook voorzitter en gedelegeerd bestuurder was van Les Etablissements Textiles Fernand Hanus
- Als gedelegeerd bestuurder de heer Baron Gaston Braun
- Als technisch verantwoordelijke de heer Paul Hebbelinck
De Union
Cotonnière was een grote spinnerij, doch een bescheidener weverij, en had voortdurend weverijen overgenomen om hun garen te verbruiken (Tissage Dupont te Ronse, …).
In 1957 fusioneert ze met de spinnerij en weverij Vincent. Ze trachtte eveneens spinnerijen in weverijen onder te brengen (spinnerij en weverij voor bedlinnen te Brugge) en in de Maïsstraat richtte ze een grote kabelrij op voor materialen ter versteviging van auto- en fietsbanden: EJB, genoemd naar één van haar oprichters, Emile Jean Braun.
Burgerlijk ingenieur en technisch verantwoordelijke bij de Union Cotonnière, Paul Hebbelynck, was er zich van bewust dat het vervaardigen van een degelijke draad een adequaat onderhoud van de machines vereiste. Hij ontwierp dan ook een mechanisch en elektrisch onderhoudsatelier alsook een onderzoekslaboratorium inzake spinnerij.
In 1960 verhuisden de kantoren en opslagplaatsen voor de stoffen naar een nieuw pand, zeer gunstig gelegen aan de uitrit Gent-centrum van de snelweg. Op de tussenverdieping bevond zich het restaurant en op de bovenverdieping het appartement van baron Braun, inclusief salon en eetkamer teneinde er hoge gasten te kunnen ontvangen.
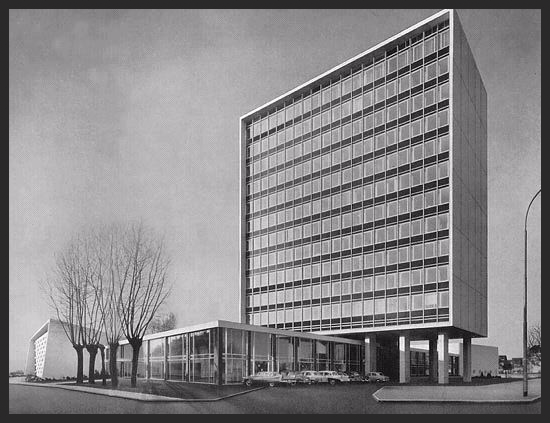
UCO toren te Ledeberg
Texas en Louisiane
Afgevaardigd bestuurder Jacques Voortman had een spinneropleiding genoten te Verviers en had vooral de ambitie kwaliteitsvolle draden en stoffen te produceren. Wat het geweven materiaal betrof, deed hij een beroep op een gerenommeerde, Franse styliste voor de creatie van kwaliteitsvolle katoenen blouses en hemden. In 1957 fusioneerde Texas met La Louisiane. Die beschikte over een grote katoenspinnerij en –weverij en over een confectieafdeling. Voortman was een uitmuntend financier en in 1963 nam hij de groep Bartsoen en Buysse over. De groep bezat een weverij voor fantasieartikelen in Ardooie en het bedrijf “Teintures et Apprêts de l’Escaut” (TAE), dat zowel een ververij, een loondrukkerij als een finishingatelier van geribd fluweel telde. TAE bezat veel onroerende goederen, die Jacques Voortman nu dus verzilverde. Het bedrijf werd in 1965 door tussenkomst van René Hanet verkocht aan de Union Cotonnière, waarvan hij toen vice-voorzitter was. René Hanet was eveneens voorzitter en afgevaardigd bestuurder van de Etablissements Textiles Fernand Hanus.
Les Établissements Textiles Fernand Hanus, onder leiding van René Hanus/Hanet.
De jongste zoon van Fernand Hanus, René Hanet-Hanus, had een spinneropleiding genoten in Roubaix. Met de opkomst van de synthetische vezels in België bouwde hij een reeks katoenspinmachines om, teneinde er nylon mee te kunnen bewerken. De nylonstoffen werden gebruikt voor het polijsten van glas. In het veredelingsatelier werden kreukvrije katoenen stoffen vervaardigd, wat in België een primeur was. Deze stoffen werden verkocht onder de naam Imutex en waren bestemd voor de productie van kinderkleding. Ze kenden zowel in België als in Duistland een groot succes. Met de winsten liet Hanet een high bulk-acrylspinnerij bouwen voor breigoederen. Vervolgens liet Hanet de katoenspinmachines omvormen om er draden mee te vervaardigen van een mengeling van katoen en polyestervezels. Dit soort draden was breukbestendig en leverde kreukvrije stoffen (voor bedlinnen en hemden). Stoffen bestaande uit synthetische vezels vereisten echter andere veredelingsmachines en – producten (voor het bleken, het verven en de finishing).
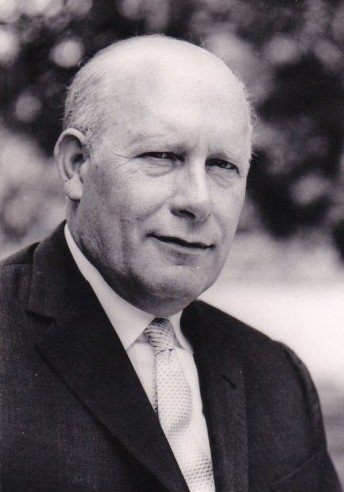
René Hanus / Hanet
Hij gaf zijn derde zoon Jacques Hanet, ingenieur textiel en scheikunde, en verantwoordelijk voor de weverij en veredeling, de taak om procedés te ontwikkelen voor het sterken, bleken, verven en veredelen van synthetische garens en weefsels in samenwerking met kleurstoffabrikanten en leveranciers van scheikundige- en sterkproducten.
Om dit te realiseren werd een klein labo gebouwd voor controle en research. Dit had tot doel:
- Het sterken: Er werd een labogetouw gebouwd met variabele snelheid om verschillende sterkproducten uit te testen. De beste resultaten op katoen werden bekomen met ester en ether derivaten van zetmeel. Deze sterkproducten waren minder gevoelig voor de variaties van de vochtigheid, die men kan bekomen in een slecht geconditioneerde weefzaal. Voor synthetische garens werden de beste resultaten bekomen met polyvinylalcohol en acrylaten.
- Het bleken: Synthetische weefsels kunnen niet gebleekt worden met conventionele bleekmiddelen, de enige mogelijk was chloriet. De ontstane gassen bij dit procedé zijn zeer ongezond en corrosief voor gewone inox. In samenwerking met de Duitse firma Kusters werd een eerste gesloten continu installatie op punt gesteld.
- Het verven:
- Verven van polyestervezel: voor het verven van polyester gebruikt men kleurstoffen, die doordringen in de vezel bij hoge temperatuur. Dit gebeurt door middel van een foulard gevolgd door een hotflue. Voor katoen was de goedkoopste manier verven de padsteam.
- Verven van polyester/viscose: aangezien de viscose bij het verven niet mag platgedrukt worden wordt er geverfd in een gesloten haspelkuip op hoge temperatuur maar deze methode verbruikt zeer veel water. Daarom werd op een nieuw verfapparaat van THIES geverfd dat uitgevonden was door GASTON COUNTY, en 6 maal minder water verbruikte.
- Verven van High bulk acrylgaren: Dit garen verhoogt in volume in heet water waardoor het een wolachtig aanvoelen bekomt. Met basische kleurstoffen bekomt men een briljant aspect. Men kan dat garen alleen verven in strengvorm in haspelkuipen. Aangezien er daarvoor veel water nodig is liet men dit garen verven in een oude ververij in Wetteren die door René Hanet was gekocht.
Om de recepten te maken voor deze vervingen, zijn de nodige laboapparaten aangeschaft voor het labo in Laarne. Tot voorheen werden de recepten gemaakt door de kleurstof-fabrikanten, die profiteerden van deze situatie om hoge prijzen aan te rekenen voor de kleurstoffen. Door zelf de colorindex van de kleurstoffen op te zoeken en zelf recepten te maken, kon men de concurrentie tussen de verschillende kleurstofleveranciers laten spelen. Door het opmaken van 3-maandelijkse provisies voor de aankoop kon men de prijzen van kleurstoffen en chemische producten met 20 tot 40% doen dalen. Tevens werden de stocks sterk verminderd.
René Hanet bouwde in Ledeberg een weverij om tot een confectie van lakens en kocht in Sint-Amandsberg een confectie voor hemden.
In 1962 koesterde René Hanet het verlangen de voormalige fabriek van zijn vader, “Les anciens Etablissements Bertel” in Rouen, terug te kopen. Hij stuurde dan ook zijn zoon Jacques naar Rouen om een eventuele overname te bestuderen. Tot zijn grote verwondering dateerden de machines grotendeels van vóór 1930, t.t.z. deze waren aangekocht door de Etablissement Textile Fernand Hanus. Het katoen werd er aangeverfd zoals wol, dus op losse vezel, en nadien geopend en gesponnen. De laineermachines waren om katoen te ruwen. Deze installaties lieten toe aan Fernand Hanus om te leveren aan het Franse leger. Aangezien de kleur blauw was heeft Fernand Hanus dus waarschijnlijk de nieuwe kleurstoffen indanthreen blauw van BASF (1901) en hydroon blauw (1908) gebruikt. Indigo kleurstof was niet goed omwille van de slechte echtheden.
De geleverde stoffen voor het Franse leger werden geconfectioneerd in zijn atelier in La Lande Glecy.
Deze stoffen waren voorzien voorzien voor gelaineerde hemden.
Een groot aantal arbeiders was van Vlaamse afkomst. (Waarschijnlijk waren hun ouders meegekomen met Fernand Hanus.)
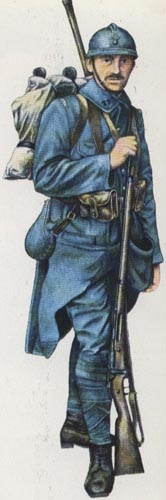
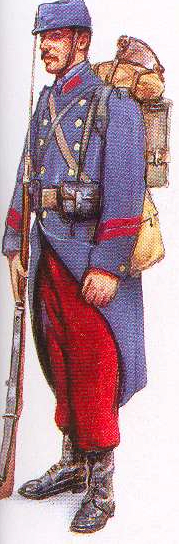
Gedurende oorlog Vóór 1914
1914 - 1918
Aangezien het te veel zou kosten om de fabriek te moderniseren en het geld beter zou geïnvesteerd worden in de weverijen en veredeling van Hanus, heeft René Hanet, als ondervoorzitter en grootste aandeelhouder van de UNION COTONNIERE, de overname laten doen van de firma BERTEL. Voor de UNION COTONNIERE was dat een middel om de Franse markt binnen te dringen.
In 1965 werd Europa overrompeld met indigo geverfde bluejeans en geribd fluweel uit de Verenigde Staten. René Hanet zond zijn zoon Jacques Hanet naar de USA om dit te bestuderen.
Hij stelde vast dat de jeans op een primitieve manier werden geverfd, namelijk in kabelvorm. Dit vroeg een groot aantal bewerkingen.
Daarom zocht Jacques Hanet een nieuw procedé om het garen in volledig continu te verven en te sterken.
Voor de geribde weefsels vroeg Jacques Hanet zijn vader om TAE (Teintures et Apprêts de l'Escaut) te laten kopen door Union Cotonnière. Het was een oude veredeling met een drukkerij en een veredeling voor geribd fluweel. Aangezien men bij Union Cotonnière geen kennis had van scheikunde vroeg men Jacques Hanet om deze veredeling te besturen.
In 1965, na de overname van TAE, vertrouwde de Union Cotonnière de “aankoop” toe aan Jacques Hanet, dit voor de aankoop van chemische producten voor TAE, voor de draadververij en voor de sterkingproducten voor de Union Cotonnière. De aankoop gebeurde op basis van driemaandelijkse prognoses, die in een pakket werden samengevoegd met de aankopen van de Etablissements Textiles Fernand Hanus.
De oorsprong van de fusie van de 3 belangrijke katoenfabrieken
Namelijk UNION COTONNIERE, LOUTEX NV en de ETABLISSEMENTS TEXTILES FERNAND HANUS.
De jongste zoon van Fernand Hanus, René Hanet, had zelf 3 zonen : Fernand (1931), Paul (1933) en Jacques (1935). Fernand werd verantwoordelijk gesteld voor de spinnerijen, Paul werd commercieel directeur van de weverijen en Jacques technisch directeur, verantwoor-delijk voor de weverijen en veredelingsateliers (bleken – verven – finishing). In 1964 stelde René Hanet aan Jacques Voortman, CEO van Loutex, een uitwisseling van bestuurders voor tussen de Etablissements Textiles Fernand Hanus en Loutex, waar Voortman op inging. Aanleiding van dit voorstel was het feit dat de Loutexaandelen van Aline Hanus bij het overlijden van haar kinderen, naar de kinderen van René Hanet zouden overgaan, aangezien zijzelf geen nakomelingen had. In 1964 werd Fernand Hanet benoemd tot bestuurder van de Union Cotonnière. Drie jaar later besliste René Hanet zich als bestuurder van Loutex terug te trekken en stelde het ambt voor aan zijn jongste zoon Jacques. Ten gevolge van dit voorstel opperde Jacques Voortman de mogelijkheid om de 3 katoenfabrieken te laten fuseren. Maar René Hanet ketste dit af, omdat hij er zeker van wilde zijn zelf het management van zijn onderneming in handen te houden. Eind 1967 zwichtte hij dan toch voor het voorstel omwille van ernstige gezondheidsproblemen, - hij had in 1954 een hartinfarct gehad -, maar wel onder de volgende voorwaarden:
1) hij zou de 3 ondernemingen leiden en hoofd worden van het directiecomité;
2) zijn 3 zonen zouden in het comité zetelen.
3) de weverijen zouden onder zijn bevoegdheid vallen.
De fusie van de N.V. Union Cotonnière met de N.V. Loutex en de N.V. Etablissements Textiles Fernand Hanus.
Op december 1967 ging de Union Cotonnière een fusie aan met Louisiane-Texas (Loutex) en met de Etablissements Textiles Fernand Hanus. Voortaan waren de 3 ondernemingen verenigd onder het letterwoord UCO.
Aangezien de Etablissements Textiles Fernand Hanus de belangrijkste aandeelhouder was van de Union Cotonnière, werd René Hanet voorzitter van het directiecomité. De Generale Maatschappij nam als tweede aandeelhouder het voorzitterschap waar van de Raad van Bestuur. Het directiecomité telde 10 leden en bestond uit 4 algemene directiediensten.
1. Een algemene directie Administratie onder de leiding van baron Gaston Braun, ondervoorzitter van de Raad van Bestuur en tevens voorzitter van een groot aantal textielondernemingen (Filtisaf, Bertel en TAE). Hij werd bijgestaan door zijn zoon Michel en door de oudste zoon van René Hanet, Fernand. Voor de veredelingsafdeling van TAE werd hij bijgestaan door Jacques Hanet.
2. Een algemene directie Spinnerij onder de leiding van Jacques Voortman, ondervoorzitter van de Raad van Bestuur en verantwoordelijke voor de spinnerijen. Zijn schoonzoon Etienne van den Boogaerde bood hem ondersteuning voor het commerciële aspect; Paul en Philippe Hebbelynck deden dit voor het technische aspect.
3. Een algemene directie Weverij onder de leiding van René Hanet, ondervoorzitter van de Raad van Bestuur en verantwoordelijke voor de weverijen. Zijn tweede zoon Paul stond hem bij in de commerciële dienst en zijn jongste zoon Jacques in de technische dienst, de veredeling en de kostprijsberekening.
4. Een algemene directie Technische Diensten onder de verantwoordelijkheid van Paul Hebbelynck. Hij beheerde het technische aspect en de kostprijzen. Inzake spinnerij werd hij ondersteund door zijn zoon Philippe, inzake weverij door Jacques Hanet.
Doordat Jacques Hanet het enige lid was van het directiecomité dat deel uitmaakte van 3 algemene directies, werden de veredelingsafdelingen van TAE ondergebracht in de weverijen. Zo werden deze 3 directies op papier herleid tot 2 directies op het terrein (spinnerij en weverij).
In december 1967 beschikte de algemene directie Spinnerij over 13 spinfabrieken en de algemene directie Weverij over 11 weeffabrieken, 4 draadververijen, een grote veredelingsfabriek voor stoffen in Laarne, een breigoedfabriek, een confectieatelier voor hemden en 2 voor bedlinnen. Het aandelenkapitaal bedroeg 1.618.860.000 Belgische frank en 3 miljard Belgische frank aan eigen reservefondsen en afschrijvingsfondsen. In totaal werden er bijna 7000 mensen tewerkgesteld.
Na de fusie maakten alle Gentse katoenspinnerijen deel uit van de UCO, met uitzondering van de Filature d’Orléans (opgekocht in 1970) en de kleine spinnerij De Porre. Hetzelfde gold voor de weverijen, met daar als uitzondering de firma nv Dierman die overgenomen werd door de Amerikaanse textielmaatschappij Milliken, nv. De Porre en nv. Van Acker. Deze twee laatste staakten hun activiteiten in 1980.
In 1971 wenste René Hanet zich om gezondheidsredenen terug te trekken als voorzitter van het directiecomité en stelde voor het voorzitterschap toe te vertrouwen aan een extern persoon, teneinde interne spanningen te vermijden. De nieuwe voorzitter, Wilfrid Matthys, was voormalig oprichter en afgevaardigd bestuurder van IBM België. René Hanet bleef echter ondervoorzitter van de Raad van Bestuur en verantwoordelijke van de algemene directie Weverij. Nadat de oude garde was vertrokken, werd de UCO in 1975 opgedeeld in 2 algemene directies : spinnerij, enerzijds, en weverij en veredeling, anderzijds. De voormalige vertegenwoordiger van de algemene directie Technische Diensten, Paul Hebbelynck, richtte in dat jaar UCO Engineering op. Deze onderneming verkocht haar knowhow inzake spinnerij en weverij aan ontwikkelingslanden. De beide afdelingen (spinnerij en weverij/veredeling) maakten daarna verschillende ontwikkelingen door.
DE NIEUWE REALISATIES VAN UCO VAN 1968 tot 1989
De grote textielrealisaties van UCO komen praktisch uitsluitend van de weverijen en veredeling. Dankzij de research afdeling van UCO Hanus Laarne onder de bevoegdheid van Jacques Hanet en in samenwerking met de Textielhogeschool en Universiteit van Gent.
Na de fusie van nv Union Cotonnière met de nv LOUTEX en de nv Etablissements Textiles Fernand Hanus, UCO genoemd, werd Jacques Hanet de technisch verantwoordelijke voor de weverij, breierij, veredeling en confectie alsook voor de kostprijsberekening van de fabrieken en de commerciële diensten.
In 1968 telde de UCO 11 weverijen, 4 garenververijen, 1 afdeling breigoederen, 1 grootveredeling voor weefsel, 2 confectie-eenheden voor bedlinnen en 1 voor overhemden. Ze telde ook een grootloon veredeling om weefsel (TAE) te bedrukken en geribd weefsel te verven. 8 weverijen deden uitsluitend aan katoenbewerking, 3 bewerkten ook deels synthetische stoffen. 70% van de geweven producten waren bestemd voor bedlinnen of overhemden. Anders dan katoen-polyesterproducten en hoogkwalitatieve overhemden en bloezen uit de Texasweverij, hadden de geweven producten zwaar te lijden onder de concurrentie van ontwikkelingslanden.
De polyester/katoen weefsel bestemd voor regenkledij ondervond grote concurrentie van gecoate katoenen- en polyamideweefsels. De polyamideweefsels voor het polijsten van glas werden niet meer gekocht, het werd vervangen door vloeibaar metaal.
De eerste bekommernis van de directie van de weverijen is om katoenweefsel, een product onder sterke concurrentie, geleidelijk te vervangen door minder concurrentiegevoelige producten zoals indigo geverfd weefsel voor bluejeans, geribd fluweel, gecoate katoenweefsels en synthetische weefsels zoals agro- en geo textiel, backing voor tapijt, en gecoate synthetische weefsels.
Oprichting in 1968 door Jacques Hanet in de geïntegreerde spinnerij/weverij/veredeling van Hanus Laarne van een centrum op voor onderzoek naar nieuwe ontwikkelingen in weverij en veredeling, in samenwerking met de Textielhogeschool. Dat gebeurde om nieuwe, niet concurrentiële en hoogtechnologische producten te kunnen ontwikkelen en nieuwe fabricageprocedés te bestuderen, die de kostprijs zouden drukken.
De vestiging Hanus Laarne bood het voordeel, dat zij over een belangrijke veredeling beschikte met alle soorten productiemachines en over een belangrijke onderhoudsdienst, waardoor prototypes en nieuwe procedés uitgetest konden worden. Bij het opkomen van de spoelloze getouwen heeft Jacques Hanet een weefzaal opgericht waar alle nieuwe types getouwen konden getest worden en samen met IBM een apparaat ontwikkeld, dat alle stilstanden op het getouw registreerde. Dat apparaat werd later gefabriceerd en gecommercialiseerd door BARCO onder de naam LOOMMONITORING. Met deze testzaal voor getouwen werd PICANOL geholpen om zijn spoelloze getouwen op punt te zetten.
De mooiste realisatie in samenwerking met Picanol in 1980 was het ombouwen van een luchtgetouw, dat tot dan toe alleen geschikt was om filamentgaren te verweven naar het verweven van gesponnen garen. Zo werd de snelheid opgedreven van 350 naar 850 scheuten/minuut. Een ware revolutie! UCO weefde eerst ribfluweel op luchtgetouwen, en later jeansstoffen. Deze evolutie heeft Picanol tot voornaamste constructeur van weefgetouwen ter wereld gemaakt.
Er werden ook nog andere studies uitgevoerd, namelijk, op het domein van:
- energiebesparing;
- automatisatie van het productieproces;
- zuivering van afvalwater en recyclage.
Deze studies hebben o.a. geleid tot:
- de oprichting van een zuiveringsinstallatie voor het afvalwater van de gemeente Laarne, en van de fabriek in Laarne;
- het recycleren van de indigokleurstof uit het afvalwater en tot de bouw van installaties voor het terugwinnen van energie. De realisaties hiervan werden later gecommercialiseerd door T.I.A. (Technical Industrial Assistance), een filiaal van UCO.
Voor deze producten waren nodig:
Dienst montageploeg en personeelsopleiding:
In 1968 richtte Jacques Hanet voor het realiseren van deze nieuwe vervaardiging, van textielproducten een dienst op « montage & opstarten van machines en personeelsopleiding ». (*) Aan het hoofd van deze beide diensten werd de voormalige directeur van de weverij van Hanus Laarne, de heer Philippe Outers benoemd en had tot taak, het plannen van de verschillende montagewerken van de machines in de fabrieken en het opleiden en opvolgen van het personeel.
Om sociale problemen te vermijden bij de reorganisatie van de weverijen was Jacques Hanet aanwezig in de ondernemingsraden van de verschillende weverijen en dit tot 1980. Deze dienst bestond uit zeer bekwame getouwregelaars, met aan het hoofd Marcel Van Acker van Laarne, een monitrice, een industrieel ingenieur elektronica, met een grote ervaring in het monteren van veredelingsmachines (Joris Demoen, voorheen hoofd van de onderhoudsdienst van Laarne en van de elektrische centrale van UCO Oudenbos), alsook een personeelschef.
Aan deze dienst was een weefzaa l(**) verbonden, waar alle types weefgetouwen werden uitgetest, zodat in samenwerking met de dienst Onderzoek & Ontwikkeling het meest adequate materieel voor nieuwe fabricage kon worden voorgesteld.
De dienst had dus als opdracht:
- het monteren en opstarten van nieuwe machines, evenals de opleiding van het nodige personeel. Een goede opleiding is noodzakelijk om de machines optimaal te bedienen en om slechte weefselkwaliteit te vermijden;(***)
- de studie van de mechanische aspecten van het materieel om beter aan de eisen van weverij en veredeling te voldoen;
- de kwaliteitscontrole van de weefgetouwen en het onderhoud van het veredelingsmaterieel;
- herstellingen in de weverijen;
- het op punt stellen van nieuwe fabricage, in samenwerking met de dienst Onderzoek &
Ontwikkeling. De mooiste realisatie was ongetwijfeld de montage van het nieuwe procedé om indigo te verven en het personeel, dat opgeleid is om te kunnen werken op de nieuwe hoog technologische machines; het is zo onder andere vrouwelijke(****) personeelsleden werden omgeschoold tot weefsters.
(*) Negen jaren later, in 1977 werd een onthaal en vormingscentrum voor de spinnerij opgericht (OVCT): drie jaren later in 1980 werd deze dienst door de VDAB (Vlaamse Dienst voor Arbeidsbemiddeling) overgenomen
(**) In deze weefzaal stelde de dienst Onderzoek & Ontwikkeling, afdeling automatisatie, samen met IBM een systeem op punt om de verschillende soorten stilstand van een getouw te registreren; dit systeem werd later geperfectioneerd door de firma BARCO.
(***) Deze vorming van het personeel is van zeer groot belang voor het in werking stellen van nieuwe machines; zeker als het gaat om nieuwe fabrieken in het buitenland. Zoniet zouden niet alleen veel stilstanden veroorzaakt worden maar vooral veel 2e keuze geschapen worden, wat het bedrijf in grote moeilijkheden zou brengen.
(****) Weven was voorheen een mannenberoep, maar het hoofd van de personeelsdienst, de heer Ronny Degryse, heeft de syndicaten overtuigd dat volledig automatische, spoelloze getouwen minder zware inspanningen vereisten zodat dit werk ook kon uitgevoerd worden door vrouwen.
Samenwerking tussen de research afdeling en de Hogeschool.
Om nieuwe producten te ontwikkelen in de veredeling van TAE waren veel textielingenieurs nodig, die een opleiding hadden gekregen in textielscheikunde. Dit werd vergemakkelijkt door de benoeming van Jacques Hanet als voorzitter van de jury voor het behalen van het diploma van technicus of technisch ingenieur in textiel in de hogeschool BTI in 1970, en later in de hogeschool voor industrieel ingenieurs CTL (chemie, textiel en landbouw) Vervolgens werden ook industrieel ingenieurs scheikunde aangeworven die een avondcursus textielscheikunde hadden gevolgd.
Om een betere samenwerking tussen Hogeschool en industrie te bekomen zocht Jacques Hanet steeds onderwerpen voor thesissen, die nuttig waren voor de textielindustrie.
De opdrachten van de directie weverijen en de nieuwe geproduceerde artikelen:
Een van de eerste opdrachten was weefsels, geproduceerd buiten UCO, over te nemen om ze af te werken in de veredeling van Hanus Laarne en de loonveredeling TAE.
Zo heeft Hanus Laarne de gelaineerde en polyester/katoenweefsels voor lakens alsook de polyester/katoenweefsels voor hemden, overgenomen. Om de kostprijs te verlagen werd een nieuw continu bleek- en verfprocedé voor lightwearweefsels(*) geïnstalleerd. Wegens de grote concurrentie in de lightwearweefsels werden deze weefsels aangekocht en vervolgens afgewerkt in de veredeling van Laarne.
De afdeling bedrukken van TAE nam de katoenen weefsels voor lakens eveneens van elders over en er werd geïnvesteerd in nieuwe drukmachines met grote breedte (machines met rotatiefilm). De veredeling van geribd fluweel werd in de weverij geïntegreerd en de oude bleek- en verfmachines werden vervangen door één belangrijke continu bleek- en verflijn, waardoor de weefcapaciteit verdrievoudigde.
De productie van twee van de drie weverijen werd achteraf samengebracht in één nieuwe weverij met nieuwe types van getouwen. Dat maakte de productie van geribd fluweel zeer competitief ten opzichte van de VS, waardoor belangrijke winstmarges mogelijk waren.
De Nieuwe producten dankzij de dienst Onderzoek en Ontwikkeling:
Een van de voornaamste producten die zeer lang onderzoek gevraagd heeft en een van de grootste uitvindingen is het verven van kettingdraden met indigo voor weefsel bestemd voor bluejeans. Het UCO/Westpoint procedé is het enige om garens te verven voor lichte jeansstoffen.
Voor meer uitleg ga naar "Oorsprong bluejeans" en "indigo procedé"
Oorsprong blue jeans
Indigo procedé
Het nieuwe indigo verfprocedé voor jeans was revolutionair,
- 1974 UCO starts up production of Indigo heavy weight denim on a continuous dyeing and slashing machine, developped in collaboration with West Point Foundry. This new dyeing process is a revolution in the world of denim and will gradually replace the American rope dyeing process.
en heeft het Amerikaanse rope-dye system bijna volledig verdrongen. Voorheen werden bijna alle jeansstoffen geverfd in de Verenigde Staten, tegenwoordig nog weinig. Het grootste deel wordt wereldwijd geverfd met het UCO – WESTPOINT procedé, dat niet alleen goedkoper is, maar ook het enige procedé, dat toelaat garen voor lichte jeansstoffen te verven.
Gedurende zes jaar bracht deze realisatie zeer veel geld op. Vanaf ca. 1980 heeft een reeks constructeurs het UCO - WEST POINT FOUNDRY procedé nagebootst. UCO lanceerde toen nog een nieuwigheid: een installatie werd omgebouwd door zijn filiaal TIA om katoenkettingdraden met alle verfstoffen continu te kunnen verven. Deze productie (color denim) was ook zeer winstgevend.
Andere nieuwe artikelen en producten:
Dankzij de dienst Onderzoek & Ontwikkeling werden nieuwe artikelen geproduceerd.
- 1968: Een nieuwe belangrijke installatie voor het coaten en bedrukken van geruwde katoenweefsels met P.V.C. en polyurethaan werd opgestart in een nieuw gebouw te Laarne.
- De keuze van de fabriek van Hanus Laarne is gemaakt omdat zij sterk gespecialiseerd was in de veredeling van het geruwde katoenweefsel.
- Deze investering werd gedaan omdat de regenmantels in polyester/katoen werden beconcurreerd door met polyurethaan gecoate katoen. Maar Jacques Hanet was vooral geïnteresseerd in het coaten van katoenweefsel met PVC, daarmee waren meer mogelijkheden. En hij wou, zoals zijn grootvader, leveren aan het leger. Daarvoor was een eigen pastabereiding nodig, zodat UCO niet afhankelijk was van leveranciers en eigen producten kon ontwikkelen, die beantwoorden aan de noden van het leger.
- P.V.C. werd gebruikt voor het coaten van katoenweefsels voor de werkkledij, voor ameublement en weefsel voor het leger. (*) Deze soort coating met haar belangrijke pastapreparatie werd uiteindelijk praktisch weinig uitgevoerd, omdat de commerciële afdelingen van UCO niet veel belang stelden in deze soort fabricage, en om de belangrijke klanten van de spinnerijen niet te ontstemmen.
- Polyurethaan werd op het geruwde katoenweefsel aangebracht voor de confectie van waterdichte kledij. Later werden ook gecoate weefsels geproduceerd voor vrouwenschoenen. Deze afdeling was zeer winstgevend. Het geïnvesteerde materieel bestond uit een grote dubbele coatinglijn, een tumbler om het weefsel te verkreukelen en een belangrijke drukinstallatie. Ook werd een zeer dure installatie gekocht om PVC-pasta te bereiden.
In 1975 werd de polyurethaancoating van SBEI overgenomen en zo werd de grote coatinglijn verdrievoudigd, dat was nodig om geitenleer na te bootsen voor vrouwenschoenen.
In 1980 werd het materieel overgenomen door de confectioneur nv SIOEN, die reeds over een kleine coating beschikte. Door zijn grote PVC-pastapreparatie was SIOEN dan minder afhankelijk van leveranciers. De lange coatingmachine stelde hem in staat zowel PVC als polyurethaan coatings te maken. Zo werd SIOEN een van de grootste PVC-coatings van België.
(*) De directie van de spinnerijen verzette zich tegen sommige investeringen van de directie van de weverijen omdat deze concurrentie zouden kunnen teweegbrengen voor de klanten van de spinnerijen. Dat heeft de UCO-weverijen sterk gelimiteerd in haar creativiteit.
-De filamentweverij en -veredeling N.V. Léon Declercq werd overgenomen, omdat de vraag naar waterdichte gecoate katoenweefsels verminderde, en werden vervangen door gecoate poliamide-weefsels. Deze weverij produceerde eveneens stoffen voor voering.
-Er werd een nieuwe coatinglijn STORCK geïnstalleerd.
-Een volledig geïntegreerde installatie voor polypropyleenweefsels werd in gebruik genomen
Vanaf 1968 werden weefsels vervaardigd met polypropyleenbandjes voor de versteviging van de bodem van rivieren en de zee, en daarna voor het stabiliseren van de bedding van banen en wegen.
In 1972 was er een geweldige schaarste aan jute voor het vervaardigen van backingweefsel voor tapijten.
Daarom zocht UCO samen met DON BROTHERS uit Groot Brittannië om de jute te vervangen door polypropyleen. Daarvoor moesten de moleculen van de polypropyleen mono-georiënteerd zijn. Dat resultaat werd bekomen door gebruik van polypropyleen van AMOCO op de extrusielijn van BARMAG. Daardoor waren Vlaanderen en Groot Brittanië de grootste regio’s voor getufd tapijt op wereldvlak.
Jacques Hanet kocht 3 extrusielijnen van BARMAG en een aantal SULZER-getouwen en liet die in een nieuwe fabriek plaatsen te Lokeren.
Vanaf 1979-1980 waren de weefsels voor geotextiel, niet alleen gefabriceerd met polypropyleen-bandjes, maar vooral voorzien van sterke filamentdraden uit polyethyleen en polyester.
- Een eerste belangrijke realisatie was een speciaal ontwikkeld polyesterweefsel voor de versteviging van de zeebodem voor de uitbouw van de zeehaven te Zeebrugge in 1979-1980.
- Berustend op een gelijkaardig procedé werd in Finland (stad Helsinki), het terugwinnen van terrein op de zee verwezenlijkt. (Een sterk polyesterweefsel werd gedurende de winter op het ijs van de bevroren zee gelegd, en beladen met stenen zodat het geheel in de lente gedurende de dooi, geleidelijk naar de bodem van de zee kon zakken, waarna het project verder kon worden afgewerkt, ).
- Een weefsel, versterkt met hoogwaardig inox metaaldraad, werd ontwikkeld om oeverbekledingen te beschermen tegen knaagdieren zoals bv ratten. (vb. vijvers van het park te Tervuren) een patent van UCO.
- Asfaltwapening voor wegen in België en Frankrijk, alsook in Abu Dhabi (Verenigde Arabische Emiraten).
- Vanaf 1986, met de achteruitgang van de markt voor Carpet Backing, werd er naar meer nieuwe ontwikkelingen gezocht:
- Wapening van gronden met weinig draagkracht (wegfundering van bv Autosnelweg A24 Lille-Nancy in Frankrijk , TGV Brussel - Parijs - vlieghaven van Singapore).
- Matras gevuld met beton als oeverbescherming of afwerking van vloeistofreservoirs (in Vietnam/Taiwan).
- Bewapening van grondmuren (Frankrijk: Boulogne - Nancy, België: Vlierzele …)
- Weefsel voor de verankering van damplaten (kanaal van de Schelde verbinding met de Ringvaart te Zwijnaarde).
- Wapening voor de bouw van kanalen (Canal des Dunes in Noord-Frankrijk).
- Aanleggen van dijken (Jamuna in Bangladesh).
De realisaties van de proefweverijen:
Het was noodzakelijk om de getouwen te moderniseren. In de proefweverij werd gezocht naar de meest performante getouwen.
Zo koos Jacques Hanet voor het weven van met indigo geverfd jeansweefsel spoelloze getouwen van SAURER DIEDERICHS.
Voor brede weefsels (3 tot 5 meter) waren de getouwen van SULZER de beste. Deze getouwen werden aangekocht voor het weven van lakens in polyester/katoen in de fabriek van Oudenbos en voor de filamentweverij van UCO Leon Declercq (LDC).
Voor het weven van brede weefsels met polypropyleen op een breedte van 5 meter in de fabriek van Lokeren, werden eveneens SULZER getouwen gekocht.
Voor het weven van geribd fluweel werden spoelloze getouwen gebruikt voor katoen die maximum 350 inslagen/minuut produceerden. Filamentgarens werden echter verweven op spoelloze luchtgetouwen van TSUDACOMA en NISSAN aan 900 inslagen/minuut. Samen met onze research afdeling is PICANOL in 1982 erin geslaagd om katoengaren voor ribfluweel en indigo geverfde jeansstoffen te weven op luchtgetouwen aan 900 inslagen/minuut. Dat heeft PICANOL aan de wereldtop gebracht in zijn branche.
Later, in 1984 werd filamentweefsel geweven op luchtgetouwen in UCO Oudenbos omdat deze getouwen meer mogelijkheden boden voor industriële weefsels dan de Sulzer-getouwen van UCO Leon Declercq.
In 1978 liet men studies uitvoeren door de researchafdeling met als doel de kostprijs van de fabriek te verlagen en producten te produceren die beantwoordden aan de vraag van de markt. Daarom stelt Jacques Hanet de directeur van de researchafdeling ook verantwoordelijk voor de kostprijsberekening.
In 1978 volgde Wilfrid Matthys de voorzitter van het directiecomité Baron Braun op. Hij werd algemeen directeur en voorzitter van Bertel en stelde Jacques Hanet aan als vicevoorzitter en afgevaardigde bestuurder van de Bertel-weverijen, met als missie dit bedrijf te herstructureren.
In 1979 sleepte het onderzoekslaboratorium een contract in de wacht om een waterzuiveringsstation te bouwen in Laarne. Het moest dienen om zowel het afvalwater van de fabriek in Laarne te zuiveren, als dat van de gemeente zelf. Het project werd grotendeels gefinancierd door de gemeente, toch werden de exploitatie en het bestuur ervan aan de UCO toevertrouwd.
In 1979 richtte Jacques Hanet TIA op om de knowhow van de UCO met betrekking tot het zuiveren van afvalwater te commercialiseren. Later zouden nog een aantal andere sectoren de commerciële toer opgaan, zoals de recyclage van energie en verfstoffen uit spoelwater, of nog de automatisering van de productieprocessen.
Eind 1979 omvatte de UCO drie katoenweverijen: één voor fluweel, één voor indigostoffen en een in Brugge, waar katoenen bedlinnen werd geproduceerd. Daarnaast maakten ook drie weverijen voor synthetisch garen deel uit van de groep: polyester-katoen voor bedlinnen, synthetisch garen (Declercq) en een vestiging voor polypropyleen.
Deze weverijen realiseerden een belangrijke omzet. Van 1968 tot 1980 maakten de weverijen grote winsten, voornamelijk dankzij de met indigo geverfde jeansweefsels en ribfluweel. De filamentweefsels van UCO Declercq en de industriële weefsels waren eveneens winstgevend.
Ondertussen gaat het er in de spinnerijen totaal anders aan toe, ze maken grote verliezen: vanaf 1975 werden de katoenspinnerijen getroffen door een zware crisis, veroorzaakt door de aanzienlijke invoer van katoenweefsels uit lageloonlanden, die meestal over katoenplantages beschikten. Tussen 1975 en 1980 heeft UCO vijf spinnerijen gesloten.
Om het aantal arbeiders drastisch te verminderen hebben de machineconstructeurs ondertussen nieuwe spinprocedés op punt gesteld. Daarbij waren vier maal minder arbeiders nodig. De gebouwen met verdiepingen van UCO waren echter ongeschikt om deze machines in onder te brengen. Om een eind te stellen aan deze situatie werd overwogen om te investeren in een systeem met open-end turbine. Wegens een te hoge kostprijs ging dit plan echter niet door.
Van 1977 tot 1982 zette de Belgische regering een textielplan op punt om de aankoop van hoogtechnologisch materieel te financieren, en zo de noodlijdende textielindustrie te redden. De financiering van UCO voor de spinnerijen kwam er in maart 1982.
Die tussenkomst bedroeg 1. 117.614.000 BEF en werd als volgt verdeeld: 299.360.000 BEF kapitaal, 419.104.000 BEF onder de vorm van een uitgiftepremie, gedekt door de emissie van geprivilegieerde aandelen zonder stemrecht; daarnaast een gedeelte als lening of kredietopening ten belope van 399.150.000 BEF, bij instellingen aan wie een intrestsubsidie van 7% toegekend werd.
In 1979 omvatte UCO acht spinnerijen, waaronder zeven voor katoen en één voor synthetische garens.
In 1980 volgde Fernand Hanet, de oudste zoon van René Hanet, de grootste aandeelhouder van UCO, Wilfrid Matthys op als voorzitter van het directiecomité. Hij zag dat de tussenkomst van het textielplan niet voldoende was om de spinnerijen te redden . Daarvoor was een fusie tussen de spinnerijen en weverijen nodig om de belangrijke reserves van de weverijen te gebruiken voor de spinnerijen.
De fusie van de 2 algemene directies spinnerijen en weverij en de research UCO Hanus Laarne van 1980 tot 1989
Fernand Hanet zocht naar een manier om de twee algemene directies samen te voegen. Zo richtte hij een permanent comité op, dat belast werd met het dagelijks bestuur. Het bestond uit twee algemene commerciële directies (de spinnerij onder leiding van Etienne van den Boogaerde en de weverij met Paul Hanet) en de Algemeen Secretaris van UCO. De directie van de fabrieken werd toevertrouwd aan de betrokken commerciële eenheden. Dit leidde evenwel tot een probleem voor de loonveredeling, die voor verschillende commerciële afdelingen werkte (UCO Print voor twee, UCO Laarne voor alle productielijnen).
De voorzitter van de bestuursraad, Robert Novis, was niet gelukkig met de voorstellen van de heer Fernand Hanet. Hij verstond niet dat Jacques Hanet uit de algemene directie verwijderd werd, want volgens hem was hij de geschikte persoon om de spinnerijen te reorganiseren. Daarvoor werd een studie gevraagd van een studiebureau uit Brussel.
Zo werd de heer Jacques Hanet aangesteld tot voorzitter van het investeringscomité. Jacques Hanet stond aan het hoofd van de afdeling R&D van de spinnerijen, de weverijen en de veredeling, en had de leiding over het personeel, dat instond voor het opstarten van nieuwe machines. Hij was tevens voorzitter van TIA, dat zich ook bezighield met het bouwen van nieuwe fabrieken en de daarmee gepaard gaande milieuproblemen. Hij werd belast met energiecontracten en de aankoop van scheikundige producten en verfstoffen.
Nadelen van de nieuwe structuur:
Het grote nadeel van deze structuur was dat de verantwoordelijken van de commerciële lijn van de weverij niet voorbereid waren om verantwoordelijk te worden voor de fabrieken. De meesten hadden nauwelijks kennis van de fabricatie in de weverij.
- Sluiting van het Etablissements Textiles de Bertel in Frankrijk. Bij het vertrek van de voorzitter directeur generaal de heer Wilfrid Mathijs moest deze normaal gezien opgevolgd worden door zijn ondervoorzitter, Jacques Hanet. Maar door de nieuwe structuur was dit niet mogelijk en aldus benoemde de voorzitter van het directiecomité Fernand Hanet de heer Etienne Van Boogaerde als voorzitter van Bertel. De spinnerij werd afhankelijk van de algemene commerciële directeur van de spinnerij en de weverij werd afhankelijk van de lijn LIGHTWEAR. De directeur generaal van Bertel, Claus, met wie Jacques Hanet de weverij in 1979 had gereorganiseerd en winstgevend had gemaakt werd afgedankt. Daardoor werd Bertel gedesorganiseerd en niet meer rendabel. Nog datzelfde jaar werd de fabriek gesloten.
- Van het grote en zeer winstgevend departement COATING dat gevestigd was in UCO Laarne werd het materieel overgenomen door de NV SIOEN. Waarom heeft UCO deze productie verkocht aan de nv SIOEN ? De commerciële directeur van de coating de heer Van Hoecke had in 1980 de pensioengerechtigde leeftijd bereikt. Omdat het permanent comité geen capabele kandidaat gevonden heeft die geïnteresseerd was om deze divisie te besturen heeft het permanent comité beslist om deze afdeling te verkopen niettegenstaande ze zeer vooruitstrevend en winstgevend was. Het is zo dat de nv SIOEN - die een grote confectie had van werkkledij en een kleine coating die gevestigd was in een oude weverij van UCO in Ardooie - geïnteresseerd was in de coating van Laarne. Zowel voor de bereiding van de PVC-pasta die hem onafhankelijk kon maken van de leveranciers, en toeliet om veel nieuwe producten te ontwikkelen, als de grote coatingmachine die zowel geschikt was voor PVC als polyurethaan en aansluitend de belangrijke drukmachine. Al de machines van de coating te Laarne werden verhuisd naar Ardooie. Zo kon SIOEN een van de belangrijkste textielbedrijven van België worden. Ze kenden een snelle groei zowel in het binnen- als het buitenland en zijn een van de belangrijkste spelers in zijn branche op wereldvlak geworden.
De voordelen van de nieuwe structuur:
Er waren twee belangrijke voordelen:
- De volledige controle over de grondstoffen en garens van de spinnerijen, die werkten voor de weverijen. (jeansweverij en fluweelweverij)
- Selectief gebruik van het geld voor het automatiseren van de spinnerijen: eerst voor de spinnerijen die werkten voor de eigen weverijen. Daarna de spinnerijen, die produceerden voor verkoop aan derden (de preparatie en spinnerij voor katoen in Ronse werd geautomatiseerd en een volledig automatische spinnerij voor polyester/katoen in UCO Rooigem).
Een volledige automatisatie van de spinnerijen was nodig om te kunnen concurreren met de lageloonlanden, die bovendien over eigen katoenplantages beschikten
De voornaamste verwezenlijking van de nieuw gestructureerde Research & Development Spinnerijen 1980-1989.
De eerste opdracht bestond erin de kosten van de spinnerijen aanzienlijk te verminderen door middel van nieuwe investeringen.
Op enkele turbinespinmachines na, open-end genaamd, was het machinepark in de spinnerijen van UCO grotendeels voorbijgestreefd. De gebouwen van de meeste spinnerijen telden verschillende verdiepingen, waardoor de behandelingskosten hoog opliepen. Door de zuilen ter ondersteuning van het plafond, was het niet mogelijk om daar zonder grote aanpassingskosten, de nieuwe volledig geautomatiseerde voorbereidingslijnen voor de spinnerij te monteren.
Om uit te maken wat het meest rendabele en meest adequate materieel zou zijn voor de verschillende spinnerijen, was het noodzakelijk om dat uit te testen, zodat een foutieve aankoop zou worden vermeden. Dit was zeker belangrijk bij de vervanging van de oude ringspinmachines door nieuwe machines. Hoewel de nieuwe spintechnologieën veel hogere snelheden haalden dan de ringspinmachines, d.w.z. vijf keer hoger voor open-end, tien keer voor airjet en vijftien keer voor frictiespinnen, was het niet mogelijk om er alle soorten garens en garennummers mee te produceren.
Zoals reeds gedaan voor de weverijen werd er een plaats gezocht om spinmachines te testen. Die werd gevonden in het controle- en onderzoekscentrum dat gevestigd was in de spinnerij Rooigem naast de spinnerij van polyester/katoen. Aan het hoofd ervan werd een industrieel ingenieur geplaatst: Vandenborre. Voor de controle van de kwaliteit werd een burgerlijk ingenieur textiel aangeworven, Jean Pierre De Leye. Die waren van groot belang om de kwaliteit van de grondstoffen goed te controleren en zo de tweede keuze in de spinnerij en de weverij te beperken.
Aan het hoofd van de afdeling stond de directeur Onderzoek & Ontwikkeling van de weverijen en veredelingen, Antoine Verroken, die in 1978 gepromoveerd was tot directeur van de kostprijsberekening in de weverijen. Hij werd bijgestaan door Lieva Van Langenhove als burgerlijk ingenieur textiel.
Uiteindelijk bleken garens gesponnen door de open-endspinmachine het best te beantwoorden aan de kwaliteitseisen van UCO, met uitzondering van de garens voor ribfluweel, de garens voor de breierij en de zeer fijne garennummers. De garens van de frictiespinmachine gaven teveel variatie in spanning en de garens van de luchtspinmachine (Murata) waren beperkt tot fijne nummers met synthetische vezels. Open-endgarens waren niet geschikt voor het weven van ribfluweel, doordat de vezelgordel in het garen het opengaan van de inslag verhinderde tijdens het borstelen.
Dankzij al dit onderzoek werden belangrijke investeringen doorgevoerd om de kostprijs van de spinnerijen te verlagen. Er werd geïnvesteerd in spinnerijen voor katoen, polyester/katoen en fibranne, die werkten voor weverijen binnen en buiten UCO.
- In een oude weefzaal in Ronse werd een volledig volautomatische katoenspinnerij van 50 ton per week geïnstalleerd. In vergelijking met een oude katoenspinnerij vergde die vier maal minder personeel. De productie van deze spinnerij was bestemd voor cliënteel.
- Aankoop van nieuwe open-endspinmachines voor het spinnen van een mengsel van polyester/katoen (in Laarne) om er polyester/katoenlakens van te maken, voorts ook bestemd voor de ketting bij de productie van ribfluweel.
- Aankoop van nieuwe open-endspinmachines voor het spinnen van katoengarens, die de oude Platt open-endspinmachines vervingen in de weverij voor indigo denimweefsel. Dit was nodig omdat de nieuwe open-endmachines twee maal sneller draaiden en volledig geautomatiseerd waren (aftrek van de bobijnen en inbrengen in een kar). Met zwaardere bobijnen konden lange ververijmonturen uitgevoerd worden. Daarna werd de preparatie van de spinnerij volledig geautomatiseerd. Zo werd het aantal arbeiders, dat er nodig was in 1970, gereduceerd van 300 naar 5, en werd de jeansfabriek van UCO de meest moderne van Europa en op technologisch vlak de eerste van de wereld.
- Installatie van nieuwe open-endspinmachines in Rooigem ter vervanging van de oude spinmachines, en een nieuwe volautomatische spinnerijvoorbereiding. Voor de installatie van deze voorbereidingslijn in de oude fabriek met verdiepingen waren zeer ingrijpende verbouwingen nodig, met extra kosten tot gevolg (voor het clienteel).
- De aankoop van twee open-endmachines en één uitrekbank (Rieter), naast zeven open-endspinmachines voor het verwerken van fibranne (minder concurrentieel). Dit garen was bestemd voor het klienteel.
- Spinnerij Galveston: een nieuwe geautomatiseerde voorbereidingslijn voor de productie van inslaggaren bestemd voor ribfluweel. Voor het spinnen van deze garens maakte men verder gebruik van de ringspinmachines omdat open-endgarens niet geschikt waren voor de inslaggarens van ribfluweel. Dankzij deze investeringen, bestudeerd in opdracht van de dienst Onderzoek & Ontwikkeling, werden de zes spinnerijen opnieuw winstgevend. Al de machines werden probleemloos geïnstalleerd en opgestart, met de medewerking van de dienst voor het monteren en inwerkingstellen van machines. Die heeft ook voor de nodige opleiding gezorgd van het betrokken personeel.
De dienst Onderzoek & Ontwikkeling in de weverijen en veredeling van 1980 tot 1989 en het oprichten van het technisch veredelings-comité.
In 1980 ondervonden de weverijen een steeds grotere concurrentie vanuit de lageloonlanden, niet alleen voor katoenweefsels, maar ook voor polyester/katoenweefsels bestemd voor kleding (light- en sportswear) en voor huishoudlinnen.
Zeer winstgevend waren wel het geribd fluweel, ondanks een lichte achteruitgang, en de indigo denimweefsels, waarvoor UCO een technologische voorsprong had opgebouwd.
De filamentweefsels in nylon (weverij Declercq) bleven nog wel winstgevend, maar begonnen voor de klassieke kledingweefsels toch een sterke concurrentie te ondervinden vanuit het Verre Oosten.
Die evolutie werd nog versneld door de introductie van Japanse luchtgetouwen (Tsudakoma en Nissan), speciaal ontworpen voor nylonfilamentweefsels, met een snelheid van 900 inslagen per minuut tegenover de 350 à 450 inslagen van de andere schietspoelloze getouwen.
De geotextielweefsels in polypropyleen en polyester (weefsels voor versterking van wegen en dijken) kenden dan weer wel een grote vooruitgang; de weefsels voor de tapijtindustrie daarentegen ondervonden een sterke concurrentie.
Een nieuwe tendens in de textielwereld was dat confectioneurs met kleine weefselvoorraden gingen werken, waardoor een snelle levering vereist was (quick respons). Dit had tot gevolg dat de verfpassen korter werden, waardoor er meer ’tweede keus’ werd geproduceerd. Om daaraan te verhelpen, ontwikkelden de Europese constructeurs verfmachines waarmee korte en middellange verfpassen snel konden worden geverfd, terwijl de hoeveelheid ’tweede keus’ toch minimaal bleef. Bovendien voelden de weefsels zachter aan, en werd een gevulder aspect bereikt dan met de continu verfmachines.
Deze nieuwe machines, jetverfmachines genaamd, hadden een aangepaste instelling naargelang van het soort weefsel: overflow of softflow om weefsels te behandelen die gevoelig waren voor plooien, lucht/waterjet om spanning van het weefsel te vermijden en een gevuld aspect te bereiken, luchtjet om een kleinere badverhouding te realiseren. Deze installaties waren ideaal voor de kledingsector (vooral voor Sportswear), zodat men zich kon verdedigen tegen de massale textielproductie van mindere kwaliteit uit de lageloonlanden.
In tegenstelling tot de weverijen en spinnerijen heeft men door de grote verscheidenheid de verschillende machines niet kunnen testen in één zaal. Daarom heeft Jacques Hanet een technisch veredelings comité opgericht, waar de verschillende fabrieken hun afgevaardigde naartoe stuurden om de beste en gepaste materialen te zoeken.
Oprichting van een technisch comité in het raam van de veredeling.
In 1980 richtte Jacques Hanet met akkoord van de directeur van de federatie veredeling, Fernand Van Causenbroeck, een technisch comité op om de verschillende processen uit de veredeling te bestuderen.
Het eerste thema was snelle levering (quick response). Daarvoor werden de verschillende methoden bestudeerd.
Daarna kwam de automatisatie van de verfrecepten (colormatching), en verder de voornaamste problemen van de veredeling.
Voor de studie betreffende het zuiveren van het afvalwater werd de directeur generaal van CENTEXBEL, Strijckman, aangesproken.
In 1979 richtte Jacques Hanet de nv TIA op, die instond voor de commercialisering van afvalwaterzuivering en automatisering. Daardoor werden veel Vlaamse veredelingen geholpen, zo werden er onder meer veertig installaties voor warmterecuperatie geïnstalleerd in de Belgische veredelingen.
De Belgische Federatie voor spinnerijen en weverijen heeft ook getracht een technisch comité op te richten, maar is daar niet in geslaagd.
Later heeft de vereniging UNITEX, met de ervaring van het technisch veredelingscomité, dat initiatief overgenomen, waarbij aan de leden alle nieuwigheden van de textiel werden ter kennis gebracht. De huidige voorzitter van UNITEX is prof. dr. ir Marc Van Parys.
In 1983 werd Jacques Hanet aangesteld als ondervoorzitter en in 1984 werd hij voorzitter van de CRIET (Comités réunis de l’Industrie de l’Ennoblissement Textile de l’UE).
Hij was eveneens lid van het Bureau van Comitextil, dat onder meer onderhandelingen voerde over de “Multivezelovereenkomst”.
In werkelijkheid werd Jacques Hanet drie maal voorzitter van de CRIET (twee maal als plaatsvervanger van Italië en Nederland en één maal als voorzitter voor België.
Zijn eerste stap in 1983 bestond in de oprichting van een werkgroep “veredeling”, die hij voorzat, en die onderzocht welke projecten konden gefinancierd worden vanuit Europa. In dit comité zetelden alle directeurs uit de Europese centra voor textielonderzoek. Om in aanmerking te komen, moest elk project de steun krijgen van drie verschillende landen.
Volgende projecten, die geleid werden door de UCO, kregen financiële steun van de Europese Commissie :
- de automatisering van een continukatoen-polyesterverfmachine;
- de automatische inspectie van fouten in de weefsels;
- geotextielstoffen voor de aanleg van wegen in de woestijn (dit project zou toegekend worden, maar werd niet gerealiseerd).
In 1985 werd Jacques Hanet door de heer Blum, directeur generaal van COMITEXTIL, voorgedragen als vertegenwoordiger van de textiel bij IRDAC (Industrial Research & Development Advisory Comitee of the EU). Eerst werd dit aanvaard, maar in laatste instantie werd dit verworpen onder druk van het comité van de Europese textielvezels, dat werd ondersteund door de chemische industrie. De Italiaanse kandidaat werd weerhouden. Dit tot grote spijt van de heer Blum en vooral van Jacques Hanet zelf, want indien hij benoemd was, had COBEPA in 1989 nooit de researchafdeling van UCO ontbonden.
De belangrijkste realisaties van het investeringscomité en de dienst Onderzoek & Ontwikkeling 1980 - 1989
Verkooplijn Sportswear
Afdeling denim indigo
- Een van de voornaamste producten die een zeer lang onderzoek gevraagd heeft, en een van de grootste uitvindingen is, is het verven van kettingdraden met indigo voor weefsel bestemd voor bluejeans. Het UCO/Westpoint procedé is het enige om garens te verven voor lichte jeansstoffen en heeft geleidelijk het Amerikaanse verfprocedé verdrongen.
Het nieuwe indigo verfprocedé voor jeans was revolutionair,
1974 UCO starts up production of Indigo heavy weight denim on a continuous dyeing and slashing machine, developped in collaboration with West Point Foundry. This new dyeing process is a revolution in the world of denim and will gradually replace the American rope dyeing process. Voorheen werden bijna alle jeansstoffen geverfd in de Verenigde Staten, tegenwoordig nog weinig. Het grootste deel wordt wereldwijd geverfd met het UCO – WESTPOINT procedé, dat niet alleen goedkoper is maar ook het enige procedé dat toelaat garen voor lichte jeansstoffen te verven.
Voor meer uitleg ga naar "Oorsprong bluejeans" en "indigo procedé"
- Met groot succes werd het gebruik van verschillende soorten kleurstoffen op om-gebouwde indigoverfmachines (color denim) op punt gesteld. Dankzij deze belangrijke realisatie kon het kettinggaren in katoen voortaan continu geverfd en gesterkt worden met alle soorten kleurstoffen.
- Het UCO-filiaal T.I.A zorgde voor de belangrijke ombouwing van indigoverfmachines voor color denim volgens de aanwijzingen van de dienst Onderzoek & Ontwikkeling. Er werd uitsluitend UCO-personeel voor ingezet om te vermijden dat de constructeurs van textielmachines het nieuwe procedé zouden kopiëren, wat trouwens gebeurde bij het procedé voor het verven van kettinggaren in indigo.
Afdeling ribfluweel
- Ook luchtgetouwen om ribfluweel te weven werden op punt gesteld. Daarvoor werd samengewerkt met de Belgische constructeur van textielmachines PICANOL. Aanvankelijk kon op deze luchtgetouwen enkel filamentgaren verweven worden. Bovendien werd ook de snelheid voor het inbrengen van het inslaggaren verhoogd: van 250 à 300 scheuten per minuut, zoals bij andere schietspoelloze getouwen, naar 800 scheuten per minuut. Op deze zeer snelle getouwen wilde UCO ribfluweel weven, en samen met de firma SCHLAFHORST bestudeerde de dienst Onderzoek & Ontwikkeling daarom een methode om zo effen mogelijk garen te spinnen, d.w.z. garen zonder knopen en met bijna onzichtbare aanspinsels.
- Voor de inslag bestudeerde zij met PICANOL een speciaal formaat voor het riet, om te vermijden dat het inslaggaren in het kettinggaren zou blijven haken of breken. In 1982, na twee jaar onderzoek, draaiden de eerste getouwen met 800 inslagen per minuut en met een rendement van meer dan 90%. Voor PICANOL waren dit soort getouwen een groot succes.
- De calorieën, die vrijkwamen uit de windtunnels van de compressoren bestemd voor de luchtgetouwen, werden gerecupereerd voor het drogen van de garenlagen op een sterkingmachine.
- Een nieuwe geautomatiseerde continuverflijn voor polyester/katoen werd gemonteerd. Met subsidie van de Europese Unie kwam er ook een automatische controle van verfrecepten gedurende het verven. De studie werd uitgevoerd in samenwerking met de kleurstofproducent ICI en de Duitse firma MAHLO, specialist in sensoren voor textielmachines. Dit was noodzakelijk om de verschillende soorten kleurenstoffen op punt te stellen, en om de hoeveelheid ’tweede keus’ te beperken, evenals de tijd die nodig was voor het wassen na het verven.
Verkooplijn Huishoudlinnen
Automatisatie van de nieuwe roterende filmdrukmachines met automatische controle van de drukrecepten
Verkooplijn industriële weefsels
Na te hebben geïnvesteerd in 1973 in de nieuwe fabriek te Lokeren en in drie nieuwe Barmag extrusie machines, heeft Jacques Hanet samen met de jonge verantwoordelijke van de extrusie afdeling, Donckers, een labo voor controle en onderzoek gecreëerd in Lokeren.
De weefgetouwen voor katoenartikelen worden geleidelijk vervangen door brede Sulzer weefgetouwen. Vervolgens, om een betere thermische stabiliteit in de weefsels te bekomen, werd een breed spanraam aangekocht.
Dit labo voor Controle en Onderzoek te Lokeren, in samenwerking met Onderzoek en Ontwikkeling, heeft heel wat belangrijke realisaties verricht:
Geotextiel
Vanaf 1979-1980 waren de weefsels voor geotextiel niet alleen gefabriceerd met polypropyleenbandjes, maar vooral met sterke filamentdraden uit polyethyleen en polyester.
- Een eerste belangrijke realisatie was een speciaal ontwikkeld polyesterweefsel voor de versteviging van de zeebodem voor de uitbouw van de zeehaven te Zeebrugge in 1979-1980.
- Berustend op een gelijkaardig procedé werd in Finland (stad Helsinki), het terugwinnen van terrein op de zee verwezenlijkt ( Een sterk polyesterweefsel werd gedurende de winter op het ijs van de bevroren zee gelegd en beladen met stenen, zodat het geheel in de lente gedurende de dooi, geleidelijk naar de bodem van de zee kon zakken, waarna het project verder kon worden afgewerkt).
- Een weefsel, versterkt met hoogwaardig inox metaaldraad, werd ontwikkeld om oeverbekledingen te beschermen tegen knaagdieren zoals bv ratten. (vb. vijvers van het park te Tervuren) een patent van UCO.
- Asfaltwapening voor wegen in België en Frankrijk, alsook in Abu Dhabi (Verenigde Arabische Emiraten).
Vanaf 1986, met de achteruitgang van de markt voor Carpet Backing, werd er naar meer nieuwe ontwikkelingen gezocht:
- Wapening van gronden met weinig draagkracht (wegfundering van bv Autosnelweg A24 Lille-Nancy in Frankrijk , TGV Brussel —Parijs , vlieghaven van Singapore).
- Matras gevuld met beton als oeverbescherming of afwerking van vloeistof reservoirs (in Vietnam —Taiwan).
- Bewapening van grondmuren (Frankrijk: Boulogne —Nancy, België: Vlierzele …)
- Weefsel voor de verankering van damplaten (kanaal van de Schelde verbinding met de Ringvaart te Zwijnaarde).
- Wapening voor de bouw van kanalen (Canal des Dunes in Noord-Frankrijk).
- Aanleggen van dijken (Jamuna in Bangladesh).
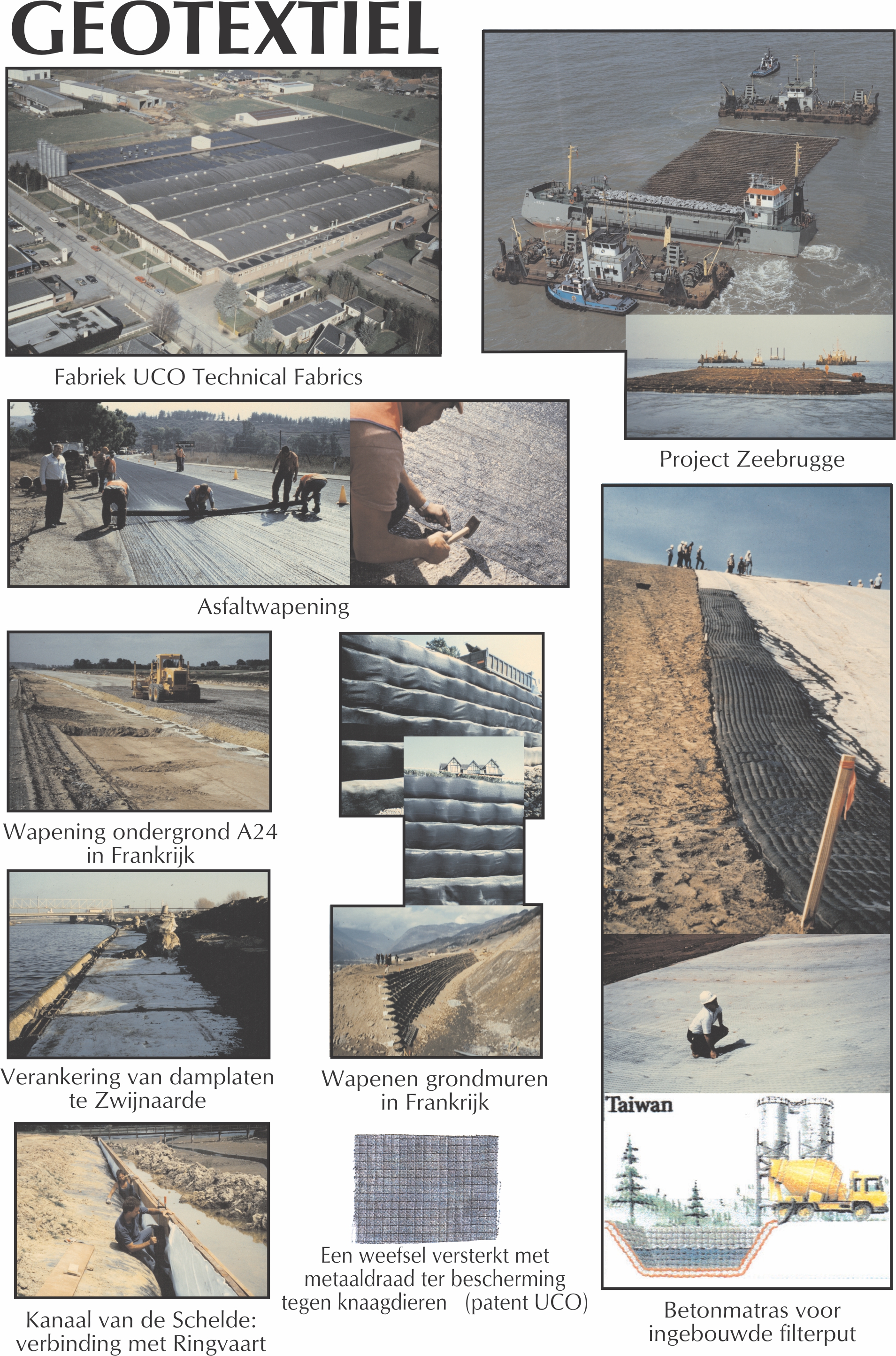
Agrotextiel en Buildingtextiel
In dezelfde periode werden ook producten ontwikkeld zowel voor de land- en tuinbouw als voor de privé- en utiliteitsbouw .
Voorbeelden hiervan zijn:
-mesttapijt voor champignonkweek, ventilatieschermen voor stallen, windschermen, insectnetten, hagelnetten, arbotainers, steigernetten, werfschermen, gewapend metselwerk, bevloeiingsmatten voor dakterrassen…..
De dienst Onderzoek en Ontwikkeling van Lokeren heeft zich na 1988 verder kunnen doorzetten dankzij de heer Donckers, de coördinator tussen het technische en het commerciële voor Nieuwe Ontwikkeling. Hij werd in 1984 benoemd als Division Manager van de industriële weefsels in 1990 en eveneens als CEO van het gefilialiseerde UCO Technical Fabric NV, en dit tot de verkoop in 1996 aan de Schotse Multinational Bonar Technical Fabrics.
De UCO Plantmanager, Desmet die Paul De Jonghe heeft opgevolgd, heeft in Lokeren verder de afdeling Research & Development ontwikkeld, en werd ook benoemd tot Plantmanger van de Agrotextielafdeling bij Bonar Technical Fabrics te Zele, dankzij het belangrijke onderzoek binnen UCO in de Agrotextiel. Hij heeft verder geo-textiel fabrieken gebouwd in Hongarije, China en Saoedi-Arabië.
De UCO Plantmanager, Desmet die Paul De Jonghe heeft opgevolgd, heeft in Lokeren verder de afdeling Research & Development ontwikkeld, en werd ook benoemd tot Plantmanger van de Agrotextielafdeling bij Bonar Technical Fabrics te Zele, dankzij het belangrijke onderzoek binnen UCO in de Agrotextiel. Hij heeft verder geo-textiel fabrieken gebouwd in Hongarije, China en Saoedi-Arabië.
Montage van een nonwovenlijn in 1980 ontworpen door UCO Onderzoek & Ontwikkeling:
Aanvankelijk moest een vlies gemaakt worden van 20 à 30 gr polypropyleenvezel en dat vlies moest aangebracht worden op een weefsel met een breedte van 5 m bestemd voor Carpet Backing. Alle bestaande nonwoveninstallaties konden een dergelijk fijn vlies niet produceren. De bedoeling was om de structuur van het weefsel te bedekken.
De enige mogelijkheid was een kaardvlies produceren, maar er bestond geen enkele kaarde met een breedte van 5 m; daarom werd samen met de Italiaanse constructeur FOR een kaarde gebouwd die twee vliezen produceerde met een breedte van 250 cm, die men naast elkaar kon plaatsen om een vlies van 500 cm breedte te bekomen.
Met het nieuwe procedé konden eveneens alle gewenste vliesdiktes geproduceerd worden door een vliesplooier toe te voegen. Deze zeer speciale nonwoven stoffen kenden eveneens een groot succes in geotextiel.
In 1992 werd door UCO het bedrijf SCI uit Noorwegen nonwoven geotextiel aangekocht.
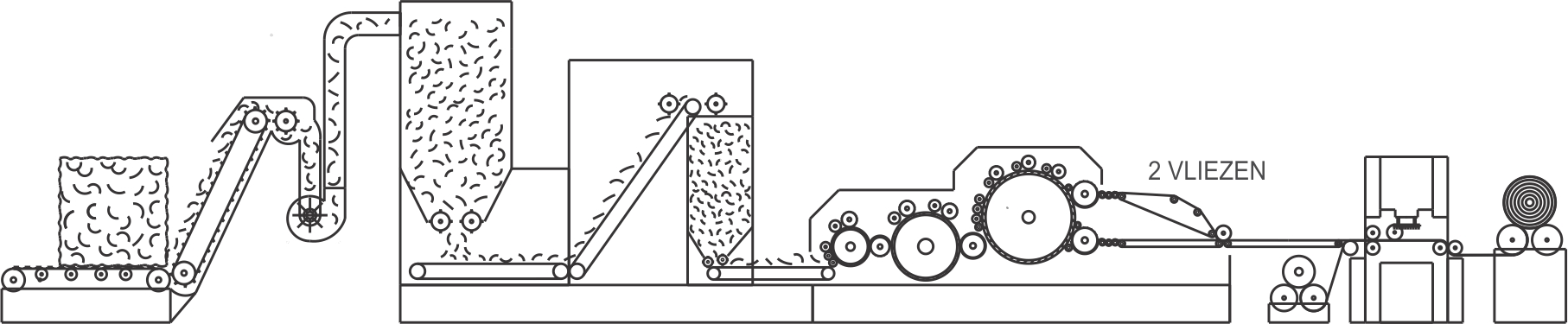
balenopener vezelaanvoer kaarde backing vernaalden oprollen
aanvoer backing+vlies
Veredeling Laarne
Realisatie van een volledig geautomatiseerde garenververij, computergestuurd, met energierecuperatie en color matching voor het bestuderen van de verfrecepten.
Wegens de sterke terugval van de bestellingen in bobijngeverfd garen besliste UCO om deze activiteiten te concentreren in de ververij van Laarne. Door de aanwezigheid van een zeer winstgevend waterzuiveringsstation en de aankoop van een vijver (7 ha groot en 15 m diep) met excellente waterkwaliteit was de vestiging in Laarne uiterst geschikt om tot een grote veredeling te worden uitgebreid.
Om een zeer competitieve ververij te kunnen realiseren, zorgde de dienst Onderzoek & Ontwikkeling met de hulp van het Zwitsers elektronicabedrijf BECATRON voor de volledig automatisatie van de verfapparaten. Bovendien werd alle vrijgekomen warmte-energie gerecupereerd. Deze twee verwezenlijkingen (automatisatie en energierecuperatie) werden door T.I.A. gecommercialiseerd.
De directeur van de gefuseerde bobijnververij, Jean-Marie D'Hoore, heeft veel geholpen voor de volledige automatisatie van de bobijnververij.
De nieuwe technologiebedrijven van UCO
N.V. T.I.A.
In 1979 richtte Jacques Hanet de firma T.I.A. op (Technical & Industrial Assistance) met het oog op de verkoop van de nieuwe UCO-technologieën inzake waterzuivering. In 1980 realiseerde T.I.A. een zuiveringsstation voor afvalwater, dat zowel ten dienste stond van de gemeente Laarne als van de daar gevestigde UCO-fabriek. Ward Madeleyn, verantwoordelijke voor de problemen van afvalwater en energiebeheer van UCO-T.I.A. werd verbonden aan de studie en opvolging van de werken aan het zuiveringsstation.
De exploitatie werd toevertrouwd aan T.I.A. Nadien toonden ook andere gemeenten interesse voor deze realisatie, o.a. de stad Lokeren, maar door de verkoop van T.I.A. in januari 1990 kon dat project niet gerealiseerd worden.
Het programma van T.I.A. werd uitgebreid tot andere gebieden, zoals energiebeheer en energieterugwinning, indigorecuperatie uit spoelwater, process optimalisatie en automatisatie.
T.I.A. werd verantwoordelijk voor het energiebeheer van de grootste Europese garenververij en de grootste Belgische stukververij.
De energierecuperatie was een groot succes, niet alleen in België (veertig installaties in vier jaar), maar ook in Frankrijk, Duitsland, Portugal en zelfs in China.
T.I.A. was ook van 1980 tot haar verkoop in 1990 de constructeur van de nieuwe technologie van UCO.
N.V. AREB
In 1983 kreeg T.I.A., actief in het recycleren van afval, een aanvraag van OVAM (Openbare Vlaamse Afvalstoffenmaatschappij ) om een onderzoek te doen naar het recycleren van huishoudelijk plastiekafval. Daarom werd in 1984 AREB (Afval Recuperatie Bedrijf) opgericht. De firma's UCO, T.I.A., de NIM, de GIMV, evenals het plastiekbedrijf Phormium werkten mee aan dit project. Het was noodzakelijk om het afvalwater uit het recyclageprocedé van het bedrijf te reinigen, daarom werd het bedrijf gevestigd naast het zuiveringsstation van Laarne.
De industriële activiteit van AREB bestond in het wassen en hergranuleren van bevuilde polyethyleen- en polypropyleenfolie. Het beheer en de exploitatie van het bedrijf werden aan Jacques Hanet toevertrouwd en de Industrieel Ingenieur Scheikunde, Marc Crommelinckx, werd benoemd tot directeur van het bedrijf.
De eerste zorg was het zoeken naar afvalstoffen om de machine te bevoorraden. Er moest gestart worden met afvalstoffen uit Duitsland en Nederland, waar het verzamelen en sorteren van agrarisch afval (plasticfolie) en afval van de grote winkelketens goed georganiseerd was. OVAM oefende al snel druk uit op Belgische bedrijven, winkelketens en landbouwbedrijven (landbouwfolie) om hun afval te verzamelen en te sorteren. Deze afvalstoffen werden na het wassen gegranuleerd en gebruikt voor de extrusie van zakken, buizen en platen. Later werd een nieuwe machine gebouwd om polypropyleen te verwerken in een teermengsel, dat gebruikt werd als antisliplaag op de wegen of bitumen om dakbedekking resistenter te maken.
Deze onderneming voor het verzamelen van afval heeft uiteindelijk geleid tot de oprichting van IVAGO.

Installatie van AREB voor plastiekafvalrecuperatie
(tekening door de heer Marc Crommelinckx, directeur van NV AREB, in samenwerking met de heer Joris Demoen)
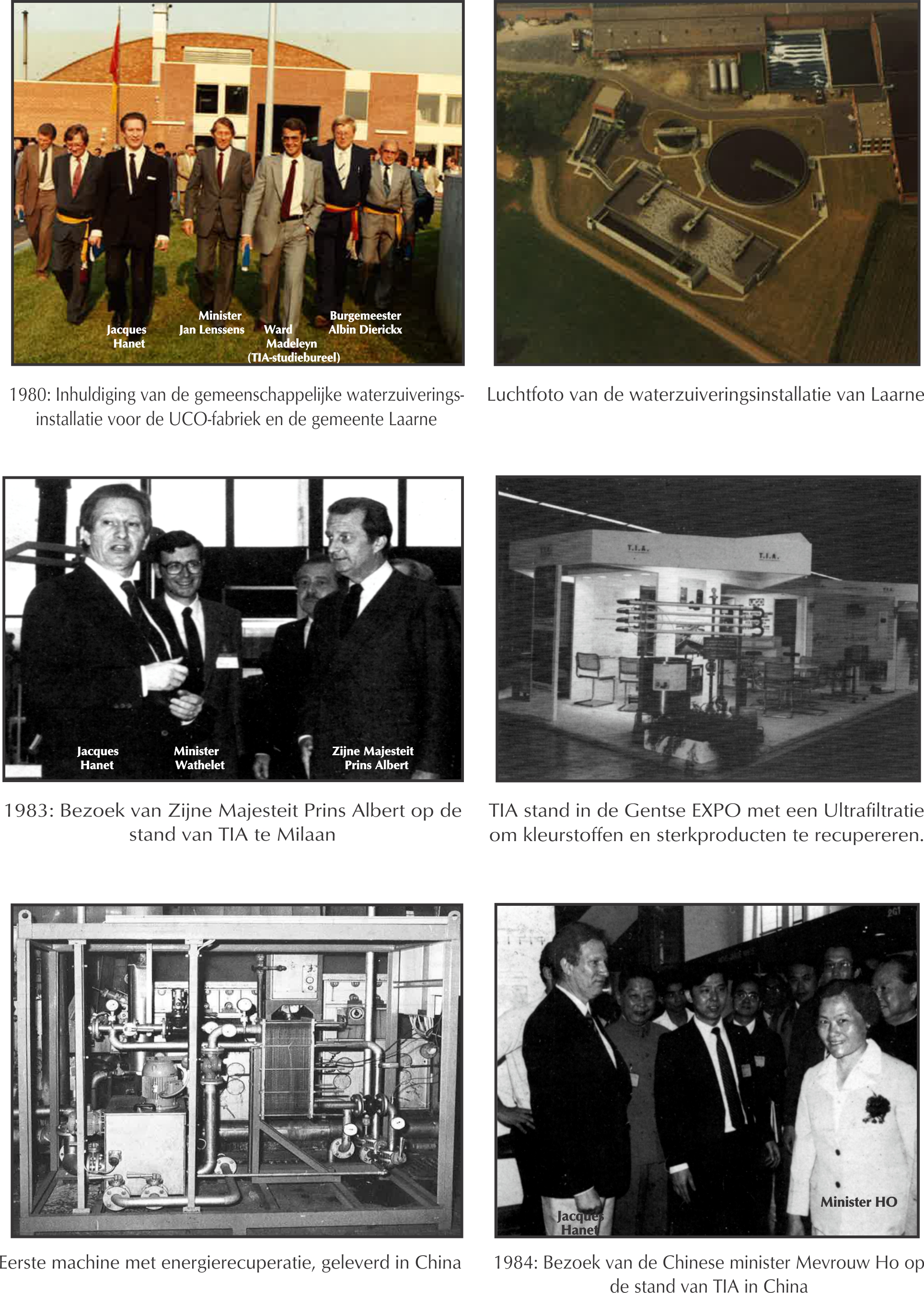
De opzoekingen van UCO gefinancierd door de Europese Commissie (IRDAC)
In 1983 werd Jacques Hanet benoemd tot vicevoorzitter en in 1984 tot voorzitter van CRIET (Comités Réunis de l'Industrie de l' Ennoblissement Textile). Hij was ook lid van het bureau van Comitextil, waar onder andere de Multivezelakkoorden besproken werden.
Zijn eerste opdracht in 1983 was de oprichting van een veredelingscomité dat de projecten onderzocht, die aan de Europese Commissie ter financiering voorgelegd zouden worden. Het comité was samengesteld uit alle directeurs van de Europese onderzoekscentra voor textiel. Elk project moest vertegenwoordigd zijn door drie verschillende landen. Jacques Hanet werd voorzitter van het comité.
In 1985 solliciteerde Jacques Hanet naar de vacante post van textielafgevaardigde binnen de Commissie Europees Onderzoek, IRDAC genaamd (Industrial Research and Advisory Commitee).
Dit met het doel de Europese Commissie te laten inzien dat het financieren van het onderzoek in de textielindustrie nodig was, daar waar belangrijke innovaties van hoog technologische producten en toepassingen in de geo- en agrosector, de bouwnijverheid, meubel- en medische industrie, beveiligingstextiel,… een opportuniteit boden.
In laatste instantie zou helaas een Italiaanse kandidaat weerhouden zijn, die een belangrijke groep in de chemische nijverheid en textiel vertegenwoordigde.
De volgende projecten onder leiding van UCO werden door de Europese Commissie gefinancierd:
- de automatisatie van een continu verfmachine voor katoen en polyester;
- de automatische inspectie van fouten in weefsels;
- de ontwikkeling van geotextielweefsels voor de wegenbouw in de woestijn. (Dit project zou goedgekeurd worden, maar werd niet uitgevoerd).
Door al deze vernieuwingen kon UCO zowel in de weverij als in de spinnerij grote winsten realiseren. Dit had tot gevolg dat twee financiële groepen geïnteresseerd waren in de aankoop van UCO-aandelen, die op de beurs genoteerd waren tegen een veel lagere waarde dan de boekhoudwaarde.
Deze twee groepen werden in 1985, na de groep Hanet, maar met een grote voorsprong op de Generale Maatschappij, de voornaamste aandeelhouders van UCO.
Zeer harde en moeilijke discussie met de leden van het directiecomité over de de veredelingen die de toekomst van de nv UCO in gevaar zouden brengen.
In 1984 sterft René Hanet, de eigenaar van de holding van de familie Hanet “La Société Gantoise de Gestion” die UCO beheerde. De holding wordt ontbonden omdat een aantal aandeelhouders (drie zonen en drie dochters) hun aandelen wou verkopen. De holding werd gesticht door René Hanet opdat zijn kinderen solidair zouden blijven.
Daar de spinnerijen in 1985 een positief resultaat vertoonden en de weverijen grote winsten genereren, wou de voorzitter van het directiecomité de veredeling afhankelijk maken van de verkoopslijnen. Dat veroorzaakte problemen voor UCO Laarne dat werkte voor de meeste verkoopslijnen en voor TAE (print en ribfluweel) dat werkte voor twee verkoopslijnen. Ook wou hij dat de veredelingen over hun eigen waterzuivering beschikten, in plaats van hun afvalwater te concentreren door ultrafiltratie en dan te lozen in de grote zuiveringsinstallatie van Laarne.
De toestand van de weverij was als volgt:
De verkoop van de effen weefsels in huishoudlinnen, en vooral die in Lightwear, liep fors terug. Nochtans was er nog een belangrijke vraag naar bedrukt weefsel en geconfectioneerd laken. Daarom fuseerden de twee verkooplijnen Lightwear en Huishoudlinnen onder één directie.
De verkoop van weefsels in ribfluweel liep terug ten voordele van de effen weefsels, die in Laarne veredeld werden. De verantwoordelijke van de verkooplijn Sportswear wou de machine om effen weefsels te veredelen overbrengen van de veredeling in Laarne naar de veredeling ribfluweel T.A.E. in Destelbergen. Tegelijk stelde hij voor, om de printmachine in de tegengestelde richting te verhuizen. Op die manier zou de veredeling T.A.E. deel uitmaken van de verkooplijn Sportswear, en de veredeling Laarne zou ressorteren onder de gefuseerde verkooplijn Lightwear-Huishoudlinnen. Dit was de wens van de commerciële directies.
De voorzitter van het investeringscomité stelde voor dat de toestand van deze twee veredelingen zou blijven zoals vroeger, en dit omwille van de volgende reden:
De verhuis van de drukkerij van TAE naar Laarne en de verhuis van de verfmachines van Laarne naar TAE was onmogelijk wegens de grote kost (ongeveer 350 mio BFr) en het feit dat TAE niet over voldoende water beschikte om de verfmachines van Laarne te bevoorraden. Een verhuis zou beide bedrijven in moeilijkheden brengen.
Een waterzuivering van de indigo ververij te Gent en in Deinze (in het midden van de stad) was niet mogelijk wegens toekomstige geurhinder. Het ware goedkoper geweest het afvalwater van het sterken en verven te concentreren door middel van ultrafiltratie (een patent van UCO), en het daarna te zuiveren in het grote waterzuiveringsstation van Laarne.
De argumenten om niet te verhuizen heeft Jacques Hanet geschreven aan de voorzitter van het directiecomité en aan de voorzitter van de beheerraad de heer Novis. De heer Novis, die burgerlijk ingenieur scheikunde was, heeft de voorzitter van het directiecomité proberen overtuigen om niet te verhuizen.
Na lange discussies in het directiecomité opteerde de meerderheid van de leden voor de verhuizing van de printafdeling van T.A.E. naar Laarne, en de aankoop van een nieuwe continu bleek- en verflijn voor T.A.E.
Van zodra de heer Novis, voorzitter van de beheerraad van UCO, het resultaat kende betreffende de verhuis van TAE naar UCO Laarne heeft hij zijn ontslag gegeven aan de voorzitter van het directiecomité en het gevraagd een koper te vinden voor zijn aandelen van de Generale Maatschappij.
Na de overname van de aandelen van de Generale Maatschappij door de Holding COBEPA-IBEL, filiaal van PARIBAS, werd het voorzitterschap van de Raad van Bestuur van UCO toevertrouwd aan een vertrouwensman van COBEPA. Het vertrek van de heer Robert Novis was een groot verlies voor UCO. Hij was niet alleen een financier, maar vooral een groot industrieel. Hij stond open voor vernieuwing en nieuwe investeringen. Als burgerlijk ingenieur in de scheikunde heeft hij de problemen in de textielveredeling altijd goed begrepen.
UCO bestuurd door COBEPA en de sluiting van de dienst Onderzoek & Ontwikkeling
Niettegenstaande de terugkoop in 1985 van de UCO-aandelen van de Generale Maatschappij door Cobepa-Ibel, wenste deze laatste nog een groter aantal aandelen te verwerven. De interesse was des te groter omdat de UCO-aandelen op de beurs veel lager genoteerd waren dan hun werkelijke waarde. Naast de familiale groepen bezaten nog twee financiële groepen een groot aantal UCO-aandelen. De voorzitter van het directiecomité de heer Fernand Hanet was belast door COBEPA om voor haar de aandelen van UCO aan te kopen. De aankoop van een gedeelte van de aandelen van de familiale groep Hanet was vergemakkelijkt door het overlijden in 1984 van de heer René Hanet. De erfgenamen van de familiale holdingmaatschappij van de familie Hanet “la Société Gantoise de Gestion” (de grootste aandeelhouder van UCO) waren de 3 dochters en 3 zonen van de heer René Hanet. Aangezien de holding was ontbonden was iedereen vrij om zijn aandelen te verkopen
Tussen 1985 en 1988 werden grote pakketten aandelen van de familiale groepen verkocht aan Cobepa-Ibel. In 1988, na lange discussie en aan een zeer hoge koers deden de twee financiële groepen afstand van hun UCO-aandelen. Zo verkregen de groep Cobepa-Ibel en de groep Vlerick (door de aankoop van aandelen, uitgeschreven door de Belgische Staat in het kader van het Textielplan) samen meer dan 50 % van de UCO-aandelen. Geen enkele familiale groep bezat nog meer dan 20 % van de UCO-aandelen.
In 1987 beschikte UCO over zeven spinnerijen voor loonwerk, waarvan vijf voor katoen en twee voor katoengaren en synthetisch garen, een geïntegreerde lijn voor fluweel, een geïntegreerde lijn voor indigo, een geïntegreerde lijn polypropyleen voor geotextiel en carpet backing, een geïntegreerde lijn voor filamentweefsels (Declercq) en in Laarne een grote veredeling en printafdeling voor loonwerk.
Met al deze afdelingen boekte UCO in 1986 grote winsten. Cobepa, de financiële groep bij uitstek binnen UCO, zocht vooral naar een hoog rendement van haar bezittingen, en bijgevolg wilde zij de UCO-gebouwen verkopen, aangezien die een grote waarde hadden op de Gentse immobiliënmarkt. Daarom werd de dienst Investeringen in de periode 1986 - 1987 belast met het verhuizen van het machinepark van de vijf spinnerijen naar de fluweelweverij van Brugge, en de verhuizing van de fluweelluchtgetouwen naar een nieuw gebouw bij de fabriek waar blauwe denim werd geproduceerd. De nieuwe spinnerij van Brugge moest garen produceren voor het cliënteel. De laatste Gentse spinnerij voor loonwerk daarentegen werkte verder voor de fluweelweverij. Naast de afdeling blauwe denim werd een nieuw gebouw opgetrokken voor de fluweelgetouwen.
De kosten voor verhuizing, inrichting, bouw en stilleggen van de productie liepen hoop op. Maar dankzij de enorme winsten, die in 1985, 1986 en 1987 gerealiseerd werden, waren deze uitgaven toch mogelijk, zij het ten koste van de dividenden voor de aandeelhouders.
In 1986 werden de machines van 5 spinnerijen verhuisd naar de fluweelweverij van Brugge, waar de beste directeur van de spinnerijen de heer Van Hoecke, voormalig directeur van Laarne, werd aangesteld als nieuwe directeur.
Nadat COBEPA, IBEL en de groep Vlerick 50% van de aandelen van UCO verworven hadden en geen van de andere aandeelhouders nog 20% bezat, wilden ze hun winst nemen door fabrieken te sluiten of te verkopen. Daarom was het nodig in 1987 om het investeringscomité van de heer Jacques Hanet en zijn dienst voor montage van nieuwe machines af te schaffen.
In 1988 werd de heer Jacques Hanet herleid tot gedelegeerd bestuurder verantwoordelijk voor research & development en CEO van de dochtermaatschappij T.I.A en AREB.
De heer Fernand Hanet werd directeur generaal. Hij stelde zijn schoonzoon, de heer Alain Vermeersch verantwoordelijk voor de afdeling Sportswear waartoe ook UCO Denim behoort. Dankzij een nieuw procedé om kettinggaren voor denim continu te verven met alle kleurstoffen, maakte deze afdeling grote winsten. Het nieuwe procedé was op punt gesteld door UCO research & development, en noodzakelijke aanpassingen aan de machines werden uitgevoerd door T.I.A.
In 1989 schafte UCO onder het impuls van Cobepa niet enkel de dienst montage, opstarten van nieuwe machines en opleiding personeel af, maar ook, ondanks het verzet van de betrokken technici, de dienst Onderzoek & Ontwikkeling.
Deze kortzichtige en louter door financiële motieven ingegeven beslissing had vooral op lange termijn nefaste gevolgen door het gebrek aan industriële visie.
Het verlies van deze twee diensten heeft de industriële activiteit van UCO sterk belemmerd.
- De ex-directeur van de dienst Onderzoek & Ontwikkeling verspreidde het indigoverfprocedé van UCO over de hele wereld (Portugal, Noord-Afrika, Turkije en vooral India). In India richtte hij één van de grootste verffabrieken voor indigo op, nl. ARVIND MILLS. Dit had tot gevolg dat de textielproducenten in de lageloonlanden, waar ook het katoen geteeld wordt, de markt overspoelden met indigoweefsel geverfd volgens het UCO-WEST POINT FOUNDRY-procedé.
- Vooral de veredelingsfabrieken verloren door het schrappen van de dienst belangrijke technische assistentie om te innoveren en hun kwaliteit te verbeteren. De afdeling denim indigo, grotendeels aangewezen op de dienst Onderzoek & Ontwikkeling, was het grootste slachtoffer.
- De verantwoordelijke van het onderzoek in de spinnerijen, alsook een paar personeelsleden van de dienst Onderzoek & Ontwikkeling van de veredelingen werden in dienst genomen door een belangrijke Belgische Sportswear concurrent van UCO (UTEXBEL).
- Na de sluiting van de controleafdeling van de spinnerijen ging de kwaliteit van het aangekochte katoen sterk achteruit. Dat had tot gevolg dat de tweede keuze in de spinnerij van Brugge geweldig steeg, en dus ook in de denimafdeling als grootste klant van die spinnerij. Daardoor gaf de directeur van Brugge, de heer Van Hoecke, zijn ontslag. Hij werd daarna aangeworven door UTEXBEL. Dankzij het personeel van UCO werd UTEXBEL de beste spinnerij van België.
- Onderzoek gesubsidieerd door de Europese Unie werd stilgelegd. Een project dat belangrijk geweest zou zijn voor de bloei van de verkooplijn Industriële Weefsels, werd opgegeven. Mevrouw Lieva Van Langenhove, rechterhand van de directeur Research & Development, verliet de firma en kort daarop werd ze benoemd tot professor aan het Departement Textiel van de Gentse Universiteit Begin1990 volgde de verkoop van de twee hoogtechnologische bedrijven in volle expansie: T.I.A. (waterzuivering, energierecuperatie en automatisatie) en AREB (afvalverwerking). Beide bedrijven zouden het UCO mogelijk gemaakt hebben zich te ontwikkelen in geavanceerde sectoren met toekomst.
Na de sluiting van de researchafdelingen van de spinnerijen en weverijen was er een grote daling in de samenwerking met de hogeschool om nieuwe projecten op te starten. Waren er in 1989 nog meer dan 100 afgestudeerde textielingenieurs, na de sluiting van de researchafdelingen daalde dit aantal drastisch. In 2014 was het aantal studenten voor het behalen van het diploma industrieel gedaald tot 5 en burgerlijk ingenieur gedaald tot 3, waarvan 2 buitenlanders.
In 1989 was na de sluiting van een aantal fabrieken veel personeel van UCO zonder werk. Dan heeft COBEPA aan de secretaris generaal en de personeelsdirecteur de opdracht gegeven om op een goedkope manier van dat personeel af te raken. Hij stelde een vertrekpremie voor aan allen, die op eigen initiatief UCO wilden verlaten. Dit had zeer negatieve gevolgen voor UCO, want het waren vooral de beste medewerkers, die op dat voorstel ingingen.
Een tweede gevolg was dat studenten niet meer aangetrokken werden tot het textielonderwijs omdat ze dachten dat textiel een product voor de ontwikkelingslanden was.
En om aan de syndicaten te tonen dat COBEPA ook personeel van de hogere directie niet spaarde werden drie afgevaardigde bestuurders afgedankt: de heer Van Boogaerde, verantwoordelijk voor de spinnerijen, de heer Paul Hanet, verantwoordelijk voor de weverijen en de heer Jacques Hanet, verantwoordelijk voor de Research. Ze bleven wel lid van de raad van bestuur.
In 1989 wou Fernand Hanet, de nieuwe directeur generaal van UCO, wat hij in 1985 gevraagd had namelijk de verhuis van de drukkerij van TAE naar Laarne en het vervangen in TAE van een zeer dure verf- en bleekinstallatie voor het verven van katoen en polyester. Alsook een zuiveringsstation voor het afvalwater van de indigoververij in Emile-Jean Braun. Dit was mogelijk omdat de verantwoordelijke voor de montage en de verantwoordelijke voor de zuiveringsstations nu onder zijn bevoegdheid kwamen.
In 1991 maakten de afdelingen fluweel waarvoor er geen vraag meer was en de recent gerealiseerde installatie voor platte weefsels (flats) grote verliezen. Het grote gebouw voor de veredeling van fluweel en flats van TAE in Destelbergen werd daarom verkocht. Ook twee jaar later werden de nieuwe bleek- en verfinstallatie verkocht aan een concurrent van fluweel.
In 1996 werd UCO in twee entiteiten opgesplitst: BELVUCO (onroerende goederen + portefeuille) en UCO TEXTILES (productie-eenheden). BELVUCO fuseerde vervolgens met IBEL (filiaal van Cobepa).
Nog steeds onder impuls van Cobepa, hoofdzakelijk een financiële onderneming, ging zij op de in 1996 ingeslagen weg voort, en probeerde ze de productie-eenheden van UCO TEXTILES zelf afzonderlijk te verkopen. Zo werd de veredeling Laarne verkocht aan de Amerikaanse multinational « Microfibres », die er zijn Europese productie- en verkoopvestiging uitbouwde. De overname van Laarne was voor Microfibres zeer gunstig, want de veredeling Laarne beschikte naast een vijver van 7 ha en 15 m diepte, ook over een zeer winstgevende zuiveringsinstallatie voor afvalwater en het nodige veredelingsmaterieel voor haar productie. Aan de Britse multinational “Bonar Technical Fabrics” werd de weverij en non-woven afdeling voor carpet backing en geotextiel in Lokeren verkocht. Dat was een zeer rendabele afdeling met zeer gunstige toekomstperspectieven.
Gedurende de periode dat Jacques Hanet bestuurder was bij UCO heeft hij er alles aan gedaan om te beletten dat de zeer technologische fabrieken van UCO verkocht werden. (UCO Laarne en de nonwoven en geotextiel in Lokeren) en heeft hij studies uitgevoerd om de fabrieken beter te organiseren (automatisering van de keurtafels en inpak in de denimfabriek)
Gevolgen van de sluiting van Controle en Research van spinnerij en weverij.
De overblijvende fabrieken van UCO werden sterk gehandicapt door de sluiting in 1989 van de R&D-afdeling.
- Controle spinnerijen omdat de kwaliteit van het katoen werd verwaarloosd, waardoor in de denim weverij en de spinnerij van Brugge veel tweede keuze werd veroorzaakt.
- Door de sluiting van de Research afdeling van de weverij en veredeling van Laarne werden de veredelingsmachines niet verder gemoderniseerd.
- Door de sluiting van TIA kon de ombouw van de indigoverfmachine voor het verven van colordenim (wat zeer winstgevend was) niet verder geautomatiseerd worden. Nadat TIA in 1990 verkocht was heeft UCO de indigoverfmachines laten maken door een Italiaanse constructeur beconcurreerd door zijn eigen procedé.
In 2001 wil de heer Alain Vermeersch, division manager van UCO Sportswear, niet dat UCO volledig zou verdwijnen en vraagt hij de heren Paul en Jacques Hanet, belangrijkste aandeelhouders van UCO om de heer Philippe Vlerick te helpen om een openbare aankoop van de aandelen van UCO te realiseren. Zo werd Philippe Vlerick in 2001 CEO van UCO, hierin bijgestaan door Alain Vermeersch.
UCO Textiles bestuurd door Philippe Vlerick en herleid tot een holdingmaatschappij.
In 2001 deed de groep Philippe Vlerick met succes een openbaar bod op de aandelen UCO TEXTILES.
Het oude UCO imperium van 1967 was op dit moment gereduceerd tot vier productiesites gesitueerd in Gent, Brugge, Lokeren-Oudenbos en Deinze. De groep beschikte niet alleen over een belangrijke fabriek voor indigo en flats in Gent, maar ook over een grote spinnerij voor katoen en polyester/katoen in Brugge en een filamentweverij (Declercq) in Oudenbos en een ververij in Deinze.
De nieuwe directie van UCO Textiles kende enorme tegenslagen.
Het afvalwater van de veredeling Declercq in Deinze voldeed niet aan de lozingsnormen, waardoor het bedrijf moest verhuizen. Door de verkoop van veredeling Laarne, was de veredeling Declercq genoodzaakt om te verhuizen naar de fabriek UCO EJB, waar blauwe indigoweefsels geproduceerd werden. De kosten voor de verhuizing en aanpassing, evenals voor de uitbreiding van de zuiveringsinstallatie, waren zeer aanzienlijk en brachten veel problemen voor de omwonenden.
Vervolgens kende UCO TEXTILES grote problemen in de afdeling indigo. De markt werd overspoeld door indigoweefsel afkomstig van o.a. lageloonlanden die het UCO procedé voor het verven van indigo toepasten. De verspreiding van het verfprocedé van de oude UCO werd vergemakkelijkt sinds de dienst afdeling Onderzoek & Ontwikkeling in 1989 gesloten werd. Sindsdien probeerde de directie van UCO TEXTILES zijn indigomarkt uit te breiden door te investeren in de Verenigde Staten, waar katoen geteeld wordt. Zij kocht er een weverij en een ververij voor indigo en integreerde er vervolgens een katoenspinnerij. Ze maakten gebruik van het oude Amerikaanse verfprocedé, dat voorbijgestreefd was en geweldig beconcurreerd werd door het UCO-Westpoint procedé.
In 2005-2006 werd in Roemenië, als lageloonland, een weverij en verflijn voor indigo opgericht om van daaruit de Oost-Europese markt proberen te veroveren. De installatie, vooral van de weverij voor indigo, verliep echter zeer moeizaam. Men beschikte niet meer over een eigen ploeg voor montage en opleiding van personeel.
De resultaten van UCO denim indigo leidden in 2006 tot het opzetten van een joint venture tussen UCO Sportswear en de grote Indische firma RAYMOND. (In India had UCO een sterke reputatie verworven dankzij de gewezen directeur van Uco Research, die het UCO procedé in India geïntroduceerd had.)
Door de zeer negatieve resultaten van UCO denim indigo werd in 2008 beslist om het Amerikaanse bedrijf evenals de Gentse productie-eenheid te sluiten. Door de sluiting van de Gentse denim-indigofabriek had de weverij Declercq in Oudenbos geen aanvoer meer voor veredeling en werd de activiteit, de knowhow en het personeel overgenomen door de firma CONCORDIA. Als compensatie kreeg UCO 20 % van de aandelen van CONCORDIA; de gebouwen en het materieel bleven eigendom van UCO.
Nog steeds in 2009 werd een jointventure-akkoord afgesloten tussen de spinnerij UCO Brugge en AVS Spinning/Sigma Spinning, met vestigingen in Spiere-Helkijn (beter bekend als de groep Lietaer). UCO werd hierdoor een portefeuillebedrijf.
UCO behield 50% van de aandelen van UCO RAYMOND, bestaande uit het Indische indigobedrijf en de UCO-fabriek in Roemenië.
BESLUIT:
In deze beschrijving wordt aangetoond hoe UCO tot belangrijke nieuwe realisaties en uitvindingen gekomen was. Het was dankzij de innige samenwerking tussen de UCO R&D afdeling en vooral de Textielhogeschool (CTL) dat UCO van 1968 tot 1989 een van de voornaamste textielbedrijven van Europa geworden was, en op technologisch vlak tot de wereldtop behoorde.
In 1989, voor de sluiting van UCO R&D, studeerden nog 100 studenten af aan het CTL, de enige school voor industriële ingenieurs textiel in Vlaanderen. Daarna is het aantal studenten zeer sterk gedaald. In 2014 nog vijf studenten, en aan de universiteit drie.
In 2015 werd de afdeling voor industriële ingenieurs gesloten, en ook op de Universiteit dreigde de vakgroep textiel te verdwijnen.
Dat is een drama, want in de textielbedrijven, die vooral klein en middelgroot zijn, is er een grote nood aan voornamelijk industriële ingenieurs die beter beantwoorden aan de vraag van de bedrijven dan de ingenieurs van de Universiteit, die waren meer geschikt voor studiesen minder om een bedrijf te laten draaien.
Bij grote textielbedrijven, zoals UCO vroeger was heeft men in samenwerking met de Universiteit de volgende studies gedaan: polypropyleen weefsel voor carpetbacking van getuft tapijt, recuperatie van energie en kleurstof uit het spoelwater, problemen met afvalwater, geotextiel...
Maar de meeste realisaties en uitvindingen waren een gevolg van de samenwerking tussen UCO Research & Development en de Textiel Hogeschool.
Waarom volgen de studenten de opleiding textielingenieur niet meer niettegenstaande Vlaanderen een zeer groot textielverleden heeft en veel textielbedrijven nog steeds aan de top staan op technologisch vlak?
- Door de sluiting van de UCO fabrieken werd de indruk gewekt dat textiel een product is voor de lageloonlanden.
- De media hebben deze indruk nog versterkt.
- Het museum MIAT exposeert machines van voor 1940 en geeft de indruk dat textiel een groot verleden heeft maar nu een product is van lageloonlanden.
Nochtans werd het meeste technologisch textiel geproduceerd in Vlaanderen, en voornamelijk door UCO in Gent.
Daarom wil Jacques Hanet een permanent museum waarin naast de grootste textielrealisatie en uitvinding, namelijk de indigo verfinstallatie, dat ook andere belangrijke textieluitvindingen, die nog steeds realiteit zijn, getoond worden.
Op die manier kunnen jonge mensen weer aangezet worden om de opleiding textielingenieur te volgen.
Ook de minister van onderwijs en cultuur zou moeten gevraagd worden om dit museum financieel te ondersteunen, want textiel is altijd belangrijk geweest voor Vlaanderen.