Hoe is het nieuwe Gentse indigoverfprocedé ontstaan?
Vanaf 1968 werd Europa overrompeld door indigogeverfde bluejeansbroeken uit de Verenigde Staten.
Het verven van katoengaren met indigokleurstof was een delicate operatie. Het procedé dat de Verenigde Staten gedurende meer dan 100 jaar hebben toegepast om katoengaren, bestemd voor broeken (jeans), zowel voor arbeidskleding als voor vrijetijdskledij, met indigokleurstof te verven is zeer omslachtig.
De moeilijkheid is dat de indigokleurstof, om katoen te verven, weinig substantiviteit heeft voor deze materie. De enige manier om katoen te verven met indigo is het katoen eerst gedurende 60 tot 120 seconden onder te dompelen in een bad van gereduceerde indigokleurstof en na het uitpersen van de geverfde draden, de gereduceerde kleurstof gedurende één tot drie minuten te laten oxideren in open lucht. Voor een goed resultaat moet deze operatie vier tot zes keer herhaald worden.
In 1920 bouwde de Amerikaanse constructeur Cocker Machine & Foundry Company een machine, die het mogelijk maakte om deze operatie continu te realiseren. Het katoengaren werd in kabels van 300 tot 500 draden samengebracht, geverfd, gewassen en gedroogd. Het is een zeer arbeidsintensief proces om de kabels opnieuw te openen, met een minimum aan garenbreuk, en om ze over te brengen op een boom. Dit vergt bovendien zeer gekwalificeerd personeel. Als er bij het openen van de kabels veel garens breken, kan dit aanleiding geven tot 10% ’tweede keus’.
In 1969 besliste de Gentse textielonderneming UCO om te investeren in de productie van indigoweefsel. Eerst dacht de commerciële dienst eraan samen te werken met de Amerikaanse Sportswear indigo denimfabrikant Graniteville, maar UCO realiseerde zich dat de Amerikaanse fabrikant goedkoper zou kunnen werken; dat het m.a.w. sowieso duurder zou uitvallen als UCO het Amerikaans procedé in Europa toepaste. De algemene technische directie van de Weverijen en Veredelingen van UCO, onder de leiding van Jacques Hanet, ging daarom op zoek naar een manier om de vijf verschillende operaties te herleiden tot één continue verf- en sterkinstallatie.
Om dit te kunnen realiseren was het noodzakelijk dat de ongeveer vierduizend draden in volle breedte over een afstand van zeshonderd meter parallel liepen. (Een draad die zich boven een andere draad bevindt, geeft aanleiding tot verfstrepen).
Daaraan waren de volgende voorwaarden gekoppeld:
In 1970 bouwde de dienst Onderzoek & Ontwikkeling(**) een kleine laboratoriummachine om samen met BASF als fabrikant van indigokleurstoffen te bestuderen hoeveel tijd er nodig was voor het absorberen en het oxideren van de kleurstof.
In 1971 zocht Jacques Hanet een constructeur om deze installatie te fabriceren. De Europese constructeurs van textielmachines vonden dit verfprocedé utopisch. De belangrijkste constructeur van textielmachines in Amerika, WEST POINT FOUNDRY was sterk geïnteresseerd in een samenwerking met de dienst Onderzoek & Ontwikkeling van UCO.
Nog in 1971 werd deze investering voorgesteld aan het directiecomité van UCO, waarvan een paar leden niet in dit project geloofden. Begin 1972 werd de investering eindelijk door het directiecomité aanvaard.
In 1974 draaide de continu verf- en sterkinstallatie tot ieders tevredenheid. Ze was ontworpen door het personeel van het UCO Atelier en de dienst Onderzoek & Ontwikkeling, samen met de Amerikaanse constructeur WEST POINT FOUNDRY. UCO heeft bovendien een installatie bedacht om de kleurstoffen uit het spoelwater te recupereren en opnieuw te gebruiken in het productieproces.De voornaamste voordelen van deze nieuwe verfmethode in vergelijking met het Amerikaanse ’rope dyeing’ verfprocedé waren:
Vanaf 1968 werd Europa overrompeld door indigogeverfde bluejeansbroeken uit de Verenigde Staten.
Het verven van katoengaren met indigokleurstof was een delicate operatie. Het procedé dat de Verenigde Staten gedurende meer dan 100 jaar hebben toegepast om katoengaren, bestemd voor broeken (jeans), zowel voor arbeidskleding als voor vrijetijdskledij, met indigokleurstof te verven is zeer omslachtig.
De moeilijkheid is dat de indigokleurstof, om katoen te verven, weinig substantiviteit heeft voor deze materie. De enige manier om katoen te verven met indigo is het katoen eerst gedurende 60 tot 120 seconden onder te dompelen in een bad van gereduceerde indigokleurstof en na het uitpersen van de geverfde draden, de gereduceerde kleurstof gedurende één tot drie minuten te laten oxideren in open lucht. Voor een goed resultaat moet deze operatie vier tot zes keer herhaald worden.
In 1920 bouwde de Amerikaanse constructeur Cocker Machine & Foundry Company een machine, die het mogelijk maakte om deze operatie continu te realiseren. Het katoengaren werd in kabels van 300 tot 500 draden samengebracht, geverfd, gewassen en gedroogd. Het is een zeer arbeidsintensief proces om de kabels opnieuw te openen, met een minimum aan garenbreuk, en om ze over te brengen op een boom. Dit vergt bovendien zeer gekwalificeerd personeel. Als er bij het openen van de kabels veel garens breken, kan dit aanleiding geven tot 10% ’tweede keus’.
In 1969 besliste de Gentse textielonderneming UCO om te investeren in de productie van indigoweefsel. Eerst dacht de commerciële dienst eraan samen te werken met de Amerikaanse Sportswear indigo denimfabrikant Graniteville, maar UCO realiseerde zich dat de Amerikaanse fabrikant goedkoper zou kunnen werken; dat het m.a.w. sowieso duurder zou uitvallen als UCO het Amerikaans procedé in Europa toepaste. De algemene technische directie van de Weverijen en Veredelingen van UCO, onder de leiding van Jacques Hanet, ging daarom op zoek naar een manier om de vijf verschillende operaties te herleiden tot één continue verf- en sterkinstallatie.
Om dit te kunnen realiseren was het noodzakelijk dat de ongeveer vierduizend draden in volle breedte over een afstand van zeshonderd meter parallel liepen. (Een draad die zich boven een andere draad bevindt, geeft aanleiding tot verfstrepen).
Daaraan waren de volgende voorwaarden gekoppeld:
- Praktisch geen variatie in torsie in het garen en geen knopen: de firma PLATT (UK) had een spinmachine type “open-end” praktisch zonder variatie in torsie met grote bobijnen zonder knopen.
- Geen variatie in de garenspanning op de bomen voor de verfoperatie; dit heeft men bekomen met het scheerrek van BARBER-COLMAN (USA).
- Regelmatige diameter van de 80 oxidatie rollen, die het garen ondersteunen in de luchtloop; dit heeft men kunnen vinden bij WEST POINT FOUNDRY (USA).
- De mogelijkheid om de spanning op het garen op de nieuwe verfinstallatie permanent te kunnen regelen.
In 1970 bouwde de dienst Onderzoek & Ontwikkeling(**) een kleine laboratoriummachine om samen met BASF als fabrikant van indigokleurstoffen te bestuderen hoeveel tijd er nodig was voor het absorberen en het oxideren van de kleurstof.
In 1971 zocht Jacques Hanet een constructeur om deze installatie te fabriceren. De Europese constructeurs van textielmachines vonden dit verfprocedé utopisch. De belangrijkste constructeur van textielmachines in Amerika, WEST POINT FOUNDRY was sterk geïnteresseerd in een samenwerking met de dienst Onderzoek & Ontwikkeling van UCO.
Nog in 1971 werd deze investering voorgesteld aan het directiecomité van UCO, waarvan een paar leden niet in dit project geloofden. Begin 1972 werd de investering eindelijk door het directiecomité aanvaard.
In 1974 draaide de continu verf- en sterkinstallatie tot ieders tevredenheid. Ze was ontworpen door het personeel van het UCO Atelier en de dienst Onderzoek & Ontwikkeling, samen met de Amerikaanse constructeur WEST POINT FOUNDRY. UCO heeft bovendien een installatie bedacht om de kleurstoffen uit het spoelwater te recupereren en opnieuw te gebruiken in het productieproces.De voornaamste voordelen van deze nieuwe verfmethode in vergelijking met het Amerikaanse ’rope dyeing’ verfprocedé waren:
- De arbeidskosten lagen ongeveer 50% lager; (zes tegenover vijftien personen per ploeg);
- De kosten voor het elektriciteitsverbruik lagen ongeveer 40% lager; (geen rebeamer, lichte aandrijving en uitpersing);
- Het water- en stoomverbruik lag ongeveer drie maal lager (zie inhoud van de baden en onderdompelingstijd). Dankzij het lage waterverbruik was het mogelijk het merendeel van de kleurstof in de spoelbaden te recupereren. UCO stelde een recuperatieprocedé op punt om de kleurstoffen in het verfprocedé te recycleren. Deze uitvinding werd later gecommercialiseerd door een dochtermaatschappij van UCO, T.I.A.;
- De arbeidsplaats was twee maal kleiner;
- Het procedé verminderde de hoeveelheid ’tweede keus’; (het openen van de kabels veroorzaakt anders veel garenbreuken);
- De nieuwe methode liet toe veel kortere en goedkopere katoenvezels te gebruiken;
- Het procedé kon zowel fijne als grove garens verven en met alle soorten kleurstof.
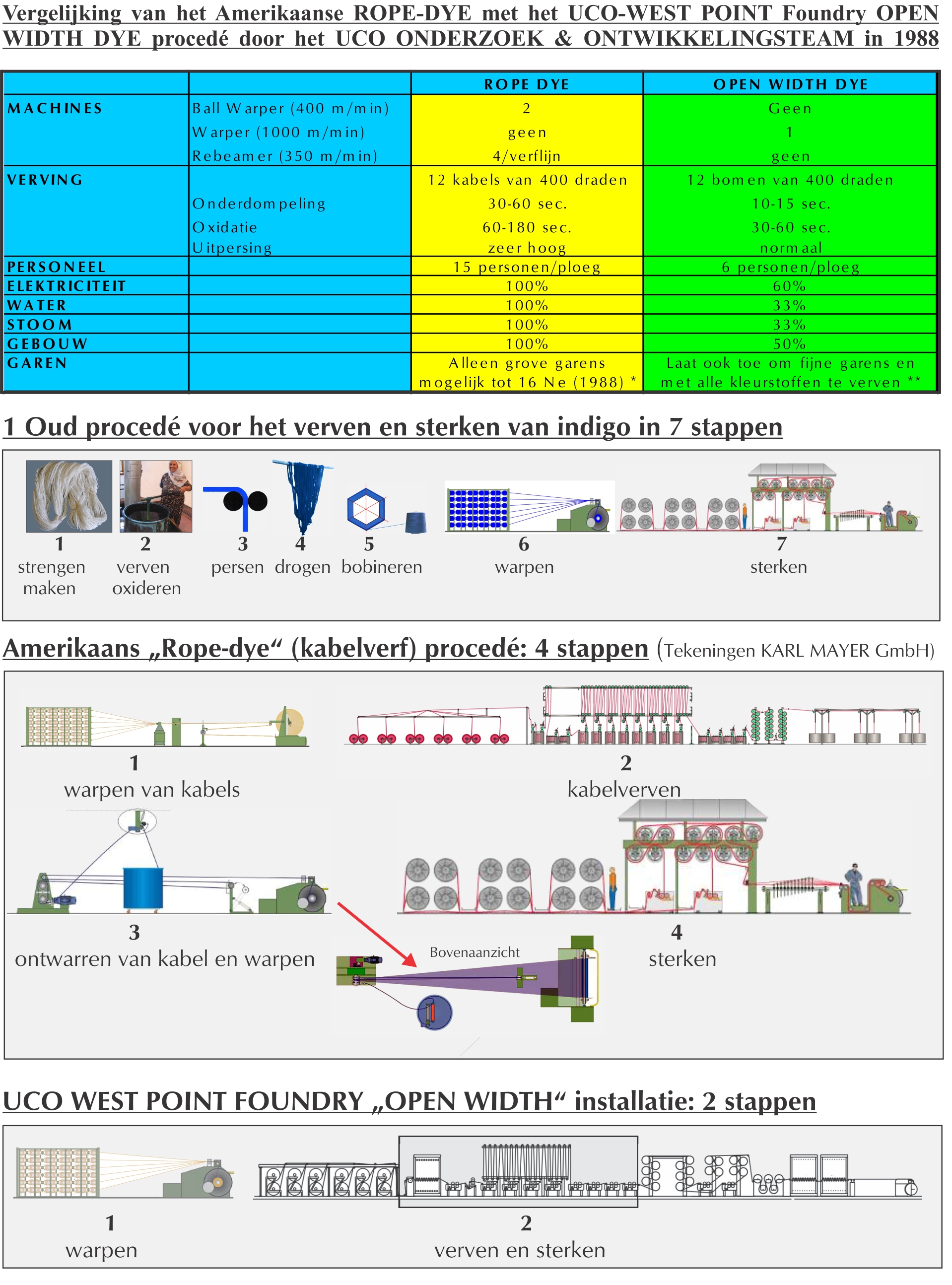
(*)Het probleem in het rope-dye procedé waren de vele garenbreuken bij het openen van de kabel. Tot 1988 was 19 Ne de limiet, nu worden fijnere garens tot 22 Ne gebruikt, mogelijk door het spinnen van garen met langer katoenvezels.(**) Een rope-dye machine is moeilijk te reinigen na een verving met sulferkleurstoffen. Daarom bouwt de rope-dye constructeur MORRISON tegenwoordig ook OPEN WIDTH machines, om alzo het kettinggaren met alle kleurstoffen te kunnen verven.
Gedurende zes jaar bracht deze realisatie zeer veel geld op. Vanaf ca. 1980 heeft een reeks constructeurs het UCO - WEST POINT FOUNDRY procedé nagebootst. UCO lanceerde toen nog een nieuwigheid: een installatie werd omgebouwd om katoenkettingdraden met alle verfstoffen continu te kunnen verven. Deze productie (color denim) was ook zeer winstgevend.
In 1989 raakte het procedé van UCO - WEST POINT FOUNDRY over de hele wereld verspreid en ging die het Amerikaanse procedé, het zogenaamde ’rope dyeing’ van Morrison, geleidelijk verdringen.
India beschikt tegenwoordig over het grootste aantal indigoverfmachines volgens het UCO-procedé. De grootste Indische indigofabrikant (waarschijnlijk de grootste ter wereld) ARVIND MILL kocht twaalf gelijkaardige installaties als UCO - WEST POINT FOUNDRY. Hij werd daarbij beïnvloed door de ex-directeur van de UCO dienst Onderzoek & Ontwikkeling, de heer Verroken. Het is niet onmogelijk dat de aankoop van de genoemde installaties er in 2006 toe heeft bijgedragen dat de belangrijke Indische maatschappij voor indigo denim, Raymond, en UCO Sportswear een joint venture hebben opgezet. Vandaag hebben een groot aantal Amerikaanse fabrikanten van indigoweefsel, die het procedé ’rope dyeing’ gebruikten, hun activiteit stilgelegd; nochtans was tot 1962 bijna 100% van de weefsels voor bluejeans afkomstig uit de USA.
Door de slinkende verkoop van de ’indigo rope dyeing’ machine heeft de Amerikaanse constructeur MORRISON recent een sheet installatie gefabriceerd voor colordenim, die berust op het UCO -WEST POINT FOUNDRY procedé.
In 1989 raakte het procedé van UCO - WEST POINT FOUNDRY over de hele wereld verspreid en ging die het Amerikaanse procedé, het zogenaamde ’rope dyeing’ van Morrison, geleidelijk verdringen.
India beschikt tegenwoordig over het grootste aantal indigoverfmachines volgens het UCO-procedé. De grootste Indische indigofabrikant (waarschijnlijk de grootste ter wereld) ARVIND MILL kocht twaalf gelijkaardige installaties als UCO - WEST POINT FOUNDRY. Hij werd daarbij beïnvloed door de ex-directeur van de UCO dienst Onderzoek & Ontwikkeling, de heer Verroken. Het is niet onmogelijk dat de aankoop van de genoemde installaties er in 2006 toe heeft bijgedragen dat de belangrijke Indische maatschappij voor indigo denim, Raymond, en UCO Sportswear een joint venture hebben opgezet. Vandaag hebben een groot aantal Amerikaanse fabrikanten van indigoweefsel, die het procedé ’rope dyeing’ gebruikten, hun activiteit stilgelegd; nochtans was tot 1962 bijna 100% van de weefsels voor bluejeans afkomstig uit de USA.
Door de slinkende verkoop van de ’indigo rope dyeing’ machine heeft de Amerikaanse constructeur MORRISON recent een sheet installatie gefabriceerd voor colordenim, die berust op het UCO -WEST POINT FOUNDRY procedé.
Color denim
Men spreekt van color denim als bij het continu kettingverven een andere kleurstof wordt gebruikt dan indigo. Door de vraag naar donkerblauwe en zwarte kleding was het noodzakelijk om zwavelzwart, al dan niet gemengd met andere tinten, toe te voegen aan de indigokleurstof.
Door de toevoeging van de zwarte kleurstof was het echter niet meer mogelijk om na het verven de indigokleurstof uit het spoelwater te recupereren (ongeveer 10% van de gebruikte kleurstof). Om een verflijn voor zwavelzwart te kunnen voorbehouden, was het noodzakelijk om te investeren in een derde installatie voor het verven van de kettingbomen met indigo. Men stelde zeer vlug vast dat de installatie, eerst bestemd voor indigokleurstof, eveneens met andere kleurstoffen kon verven zonder ombouw van de installatie. Het ging dan om de zwavelkleurstoffen zwart, bruin, beige; en na ombouw om naphthol kleurstoffen (rood), reactieve kleurstoffen (alle briljante kleuren) en indanthreen kleurstoffen (alle kleuren met uitzondering van rood).
Vanaf 1987 vroeg de commerciële dienst andere kleuren in color denim, in het bijzonder rood. Daarom moest de verfmachine omgebouwd worden. De studie werd uitgevoerd door de dienst Onderzoek & Ontwikkeling, in samenwerking met de chef van de verfafdeling, de heer Willem De Sutter. Het project werd gerealiseerd door het UCO-filiaal T.I.A. samen met zijn onderaannemers, want Jacques Hanet wilde niet dat dit procedé bekend zou worden bij de concurrentie. De garenlaag was maar tweehonderd meter lang tegenover vierhonderd meter voordien. Hierdoor werd de tijd nodig voor het wassen/spoelen, en de hoeveelheid ’tweede keus’ beperkt. Er werd een plan uitgewerkt om de installatie volledig te automatiseren. Door de sluiting van de dienst Onderzoek & Ontwikkeling begin 1989 en door de verkoop van T.I.A. in 1990 was de realisatie ervan echter niet meer mogelijk.
Men spreekt van color denim als bij het continu kettingverven een andere kleurstof wordt gebruikt dan indigo. Door de vraag naar donkerblauwe en zwarte kleding was het noodzakelijk om zwavelzwart, al dan niet gemengd met andere tinten, toe te voegen aan de indigokleurstof.
Door de toevoeging van de zwarte kleurstof was het echter niet meer mogelijk om na het verven de indigokleurstof uit het spoelwater te recupereren (ongeveer 10% van de gebruikte kleurstof). Om een verflijn voor zwavelzwart te kunnen voorbehouden, was het noodzakelijk om te investeren in een derde installatie voor het verven van de kettingbomen met indigo. Men stelde zeer vlug vast dat de installatie, eerst bestemd voor indigokleurstof, eveneens met andere kleurstoffen kon verven zonder ombouw van de installatie. Het ging dan om de zwavelkleurstoffen zwart, bruin, beige; en na ombouw om naphthol kleurstoffen (rood), reactieve kleurstoffen (alle briljante kleuren) en indanthreen kleurstoffen (alle kleuren met uitzondering van rood).
Vanaf 1987 vroeg de commerciële dienst andere kleuren in color denim, in het bijzonder rood. Daarom moest de verfmachine omgebouwd worden. De studie werd uitgevoerd door de dienst Onderzoek & Ontwikkeling, in samenwerking met de chef van de verfafdeling, de heer Willem De Sutter. Het project werd gerealiseerd door het UCO-filiaal T.I.A. samen met zijn onderaannemers, want Jacques Hanet wilde niet dat dit procedé bekend zou worden bij de concurrentie. De garenlaag was maar tweehonderd meter lang tegenover vierhonderd meter voordien. Hierdoor werd de tijd nodig voor het wassen/spoelen, en de hoeveelheid ’tweede keus’ beperkt. Er werd een plan uitgewerkt om de installatie volledig te automatiseren. Door de sluiting van de dienst Onderzoek & Ontwikkeling begin 1989 en door de verkoop van T.I.A. in 1990 was de realisatie ervan echter niet meer mogelijk.
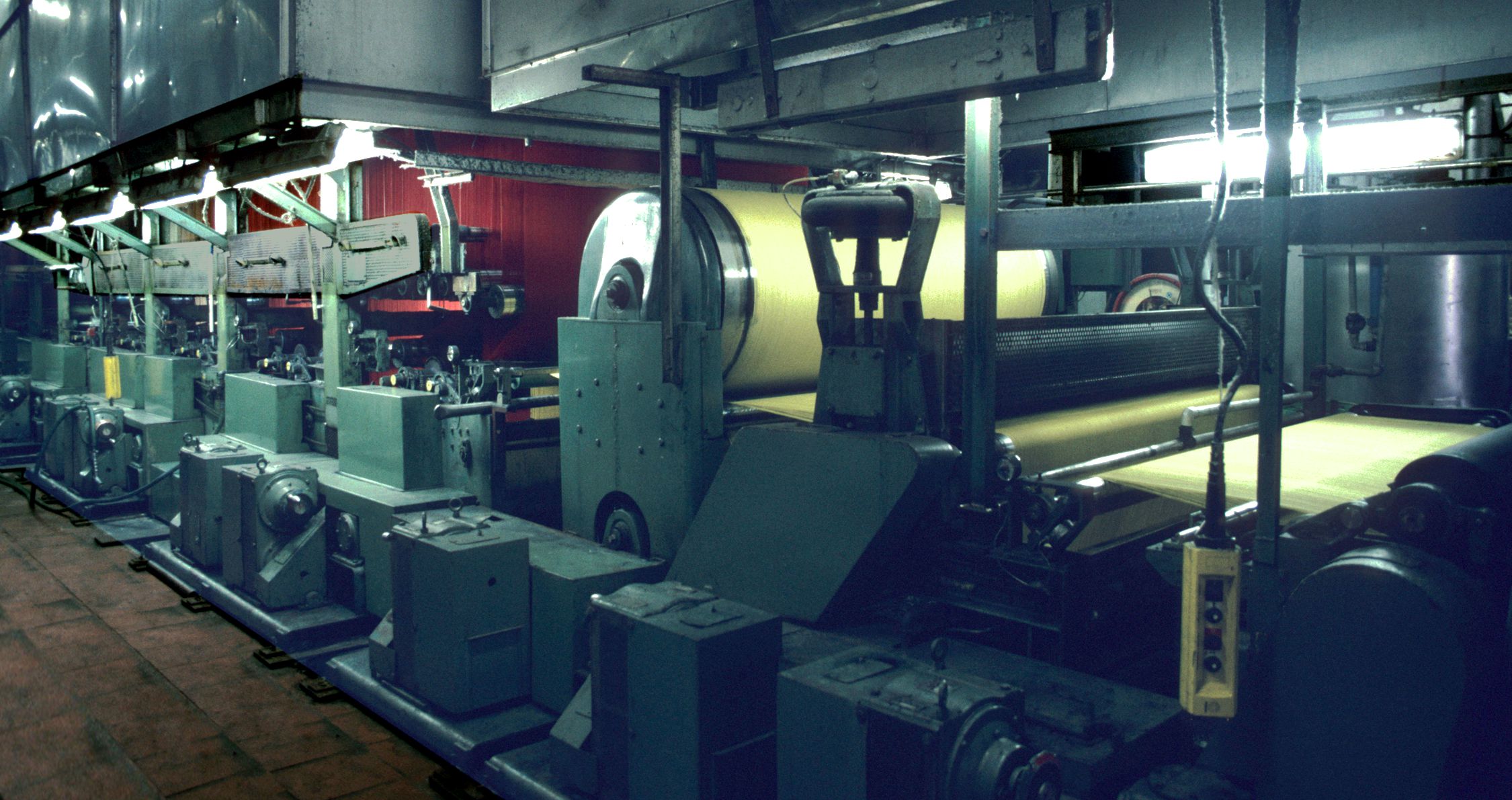
VERVEN VAN NAPHTOL KLEURSTOFFEN OP DE WESTPOINT MACHINE
Begin 1988 realiseerde de heer De Sutter zijn eerste verving met rode naphthol kleurstoffen. Vervolgens werden, geholpen door de kleurstof-fabrikant BASF, op deze installatie ook reactieve vervingen en vervingen met indanthreen uitgevoerd. Bij mijn weten was dit de eerste keer dat kettinggaren continu geverfd en gesterkt kon worden met deze drie soorten kleurstoffen.
Tot in 1989 werd het indigo verfprocedé van UCO, ’sheet dyeing’ genaamd, nog maar weinig toegepast in katoen producerende lageloonlanden zoals Turkije, India, Pakistan. Zij gebruikten het Amerikaanse procedé ’rope dyeing’, dat veel duurder was en zich beperkte tot grove garennummers. Met de sluiting van de dienst Onderzoek & Ontwikkeling van UCO heeft de directeur van deze dienst de verkoop van het indigo verfprocedé van UCO WEST POINT FOUNDRY in lageloonlanden aangemoedigd.
Door het wegvallen van de dienst Onderzoek & Ontwikkeling werd het onderzoek naar nieuwe procedés afgeremd; de automatisatie van de color denim verflijn kon niet worden uitgevoerd. Die automatisatie was noodzakelijk om de hoeveelheid ’tweede keus’ en de tijd nodig voor het wassen na het verven te verminderen; daarnaast ook om de verschillende soorten kleurenstoffen op punt te stellen. Toch heeft de chef van de verfafdeling in deze moeilijke omstandigheden (in samenwerking met de kleurstoffenfabrikant BASF) met veel moed en toewijding doorgewerkt aan de ontwikkeling van nieuwe kleurstoffen.
Met de productie van de zogenaamde « color denim » maakte UCO grote winsten, zolang zij lange partijen kon realiseren. Wegens de sterke vraag naar dit product was het noodzakelijk te investeren in een tweede installatie voor color denim. Spijtig genoeg bestond binnen UCO toen de dienst Onderzoek & Ontwikkeling niet meer. Die had deze installatie eertijds gerealiseerd, samen met de constructeur T.I.A. (verkocht in 1990).
Daarom bestelde UCO in 1990 bij de constructeur MASTER (Italië), die een sheet indigo verfprocedé op de markt had, gelijkaardig als dit van UCO, een indigo verfinstallatie om de eerste installatie UCO WEST POINT uit 1973 te vernieuwen. Vervolgens bestelde ze een tweede installatie om zowel indigo als andere soorten kleurstoffen te kunnen verven.
Tot in 1989 werd het indigo verfprocedé van UCO, ’sheet dyeing’ genaamd, nog maar weinig toegepast in katoen producerende lageloonlanden zoals Turkije, India, Pakistan. Zij gebruikten het Amerikaanse procedé ’rope dyeing’, dat veel duurder was en zich beperkte tot grove garennummers. Met de sluiting van de dienst Onderzoek & Ontwikkeling van UCO heeft de directeur van deze dienst de verkoop van het indigo verfprocedé van UCO WEST POINT FOUNDRY in lageloonlanden aangemoedigd.
Door het wegvallen van de dienst Onderzoek & Ontwikkeling werd het onderzoek naar nieuwe procedés afgeremd; de automatisatie van de color denim verflijn kon niet worden uitgevoerd. Die automatisatie was noodzakelijk om de hoeveelheid ’tweede keus’ en de tijd nodig voor het wassen na het verven te verminderen; daarnaast ook om de verschillende soorten kleurenstoffen op punt te stellen. Toch heeft de chef van de verfafdeling in deze moeilijke omstandigheden (in samenwerking met de kleurstoffenfabrikant BASF) met veel moed en toewijding doorgewerkt aan de ontwikkeling van nieuwe kleurstoffen.
Met de productie van de zogenaamde « color denim » maakte UCO grote winsten, zolang zij lange partijen kon realiseren. Wegens de sterke vraag naar dit product was het noodzakelijk te investeren in een tweede installatie voor color denim. Spijtig genoeg bestond binnen UCO toen de dienst Onderzoek & Ontwikkeling niet meer. Die had deze installatie eertijds gerealiseerd, samen met de constructeur T.I.A. (verkocht in 1990).
Daarom bestelde UCO in 1990 bij de constructeur MASTER (Italië), die een sheet indigo verfprocedé op de markt had, gelijkaardig als dit van UCO, een indigo verfinstallatie om de eerste installatie UCO WEST POINT uit 1973 te vernieuwen. Vervolgens bestelde ze een tweede installatie om zowel indigo als andere soorten kleurstoffen te kunnen verven.
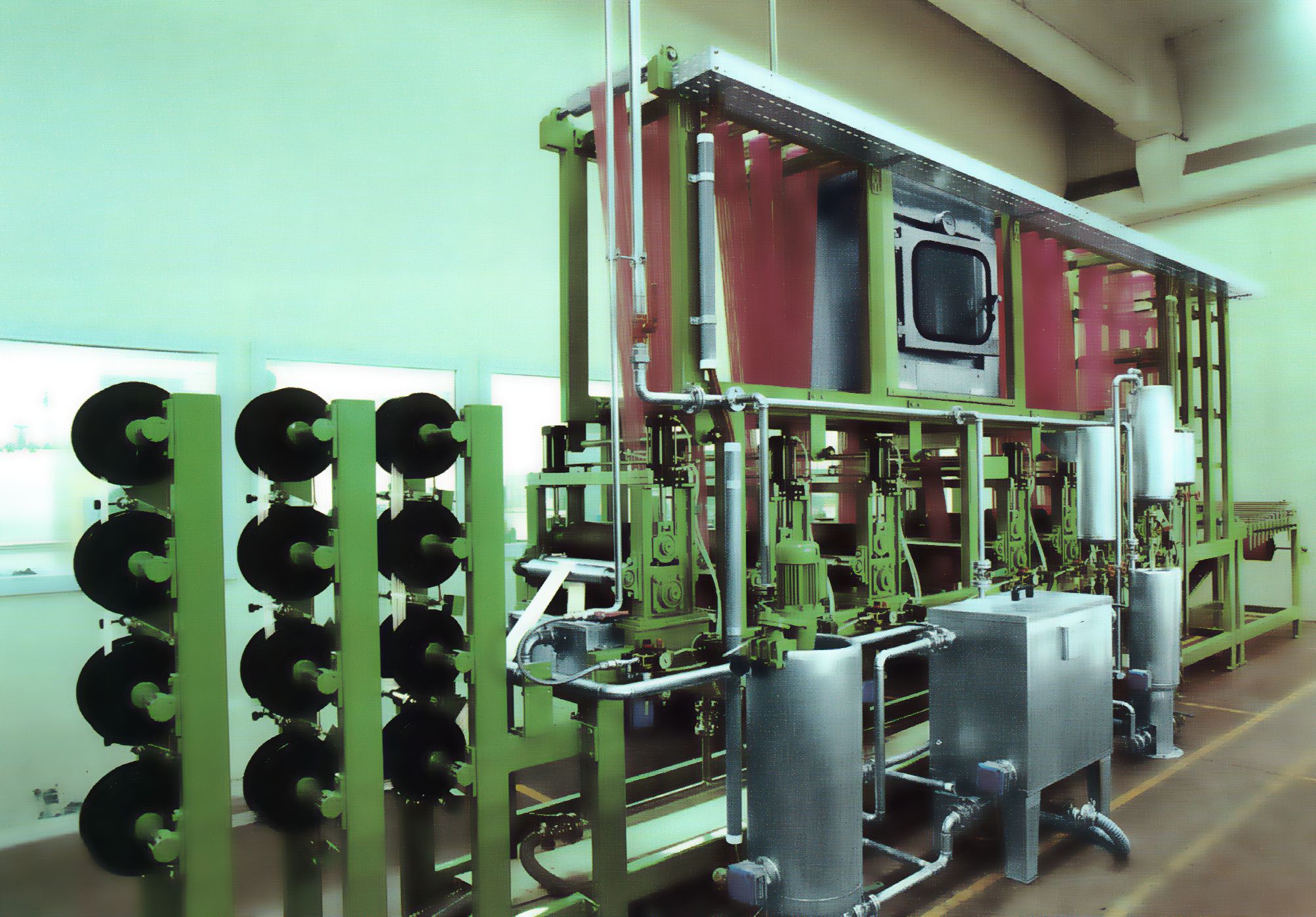
LABORATORIUMMACHINE VOOR COLORDENIM
Samen met de installaties bood de firma MASTER gratis een kleine laboratoriummachine aan om het kettinggaren continu met alle soorten kleurstoffen op punt te stellen. De MASTER machine om zowel indigo als andere kleurstoffen te verven, kampte met vele problemen bij het wassen. De garenlengte van MASTER was vierhonderd meter; tegenover tweehonderd meter bij UCO. Dat bracht een groter risico met zich van ’tweede keus’. Daarom werden de alle bestellingen (op zwart na) uitgevoerd op de UCO-installatie.
Samen met de installaties bood de firma MASTER gratis een kleine laboratoriummachine aan om het kettinggaren continu met alle soorten kleurstoffen op punt te stellen. De MASTER machine om zowel indigo als andere kleurstoffen te verven, kampte met vele problemen bij het wassen. De garenlengte van MASTER was vierhonderd meter; tegenover tweehonderd meter bij UCO. Dat bracht een groter risico met zich van ’tweede keus’. Daarom werden de alle bestellingen (op zwart na) uitgevoerd op de UCO-installatie.